What is theory and construction? This seemingly simple question unravels into a vast tapestry woven from the threads of intellectual pursuit and physical creation. From the ethereal realms of theoretical physics, where equations sculpt the universe, to the towering steel and concrete behemoths of modern architecture, the interplay between abstract thought and tangible reality defines our world. This exploration delves into the heart of this duality, revealing the intricate processes, shared methodologies, and surprising parallels between building a skyscraper and constructing a groundbreaking sociological theory.
We will journey through the meticulous stages of physical construction, witnessing the metamorphosis of blueprints into towering structures. We will then ascend to the heights of theoretical construction, where hypotheses are erected, tested, and refined through rigorous experimentation. Finally, we’ll examine the fascinating social construction of reality, exploring how shared beliefs and cultural norms shape our understanding of the world.
The journey will highlight the surprising commonalities between these seemingly disparate domains, illuminating the fundamental human drive to create and understand.
Defining “Theory”
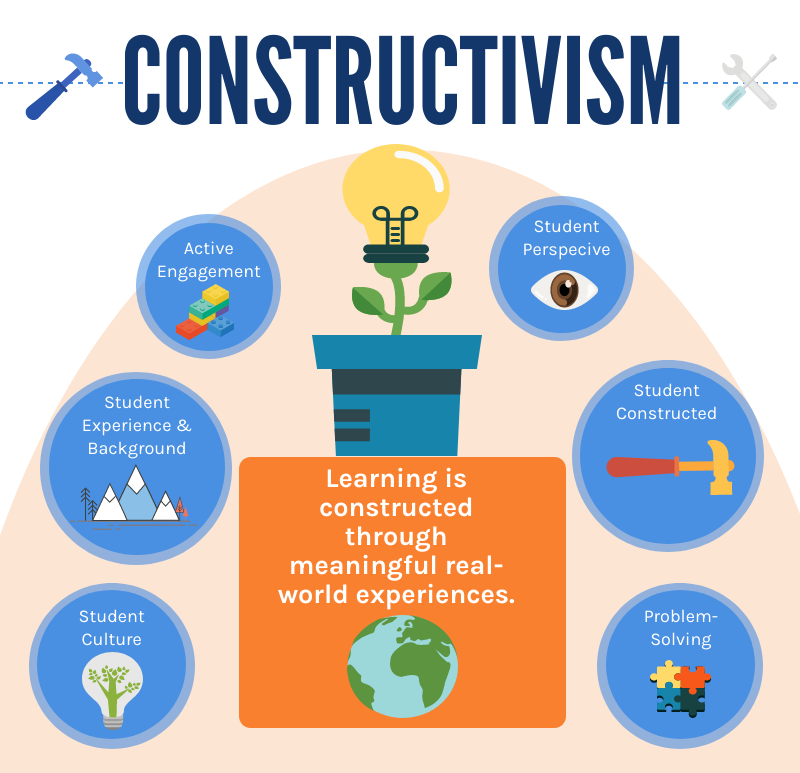
Okay, so you think “theory” means something like, “Oh, it’s just a guess, bro”? Think again. In everyday life, yeah, “theory” gets tossed around like a frisbee at a bad party – meaning a hunch, a wild speculation, something barely supported by evidence. But in the scientific world? It’s a whole different ballgame.
We’re talking serious business, the kind of stuff that can launch rockets to Mars or explain why your ex keeps showing up in your dreams (okay, maybe not that last one).The difference between a scientific theory and a casual “theory” is like comparing a finely crafted Swiss watch to a pile of rusty gears. A scientific theory is a well-substantiated explanation of some aspect of the natural world, based on a vast body of evidence and repeatedly tested and confirmed through observation and experimentation.
It’s not just a guess; it’s a robust, comprehensive explanation that has stood up to rigorous scrutiny. Think of it as a really, really solid hypothesis that’s been through the wringer and emerged victorious.
Examples of Theories Across Disciplines
Scientific theories aren’t confined to one field. They pop up everywhere, from the tiniest particles to the largest galaxies, and even in the study of human behavior. Let’s look at a few examples:In physics, we have the Theory of Relativity, which revolutionized our understanding of gravity, space, and time. Einstein’s work wasn’t just a “guess”; it made accurate predictions that have been confirmed repeatedly through experiments and observations.
Imagine trying to navigate a GPS system without it – your pizza would never arrive on time!Then there’s the Germ Theory of Disease in biology. This theory states that many diseases are caused by microorganisms. Before this theory was widely accepted, people often had no idea why they got sick. This theory led to advancements in sanitation, hygiene, and the development of vaccines and antibiotics, dramatically increasing life expectancy and improving public health worldwide.Sociology offers us Social Learning Theory, which explains how individuals learn behaviors, attitudes, and values through observation and imitation.
This theory helps us understand how social norms are transmitted and how people adapt to their social environments. Think about how trends spread through social media – that’s social learning in action!Even in architecture, we find theories at play. For instance, the theory of sustainable design guides the creation of buildings that minimize their environmental impact. This involves considering factors like energy efficiency, material selection, and waste reduction.
It’s a theory that directly influences how buildings are designed and constructed, aiming for a harmonious relationship between the built environment and the natural world.
Characteristics of a Robust Scientific Theory
A truly solid scientific theory isn’t just a collection of facts; it possesses certain key characteristics. It needs to be:* : A good theory explains a wide range of observations and phenomena. It doesn’t just describe what’s happening; it provides a mechanism to understand
why* it’s happening.
* Predictive: A robust theory allows us to make predictions about future events or observations. These predictions can then be tested, further strengthening or refining the theory.* Testable: The claims made by a theory must be testable through observation or experimentation. If a theory can’t be tested, it’s not really a scientific theory.* Falsifiable: A crucial aspect of a scientific theory is that it must be potentially disproven.
If a theory can’t be shown to be wrong, it’s not very useful scientifically. Think of it as a theory that’s so robust it can withstand attempts to disprove it.* Parsimonious: A good theory is simple and elegant, avoiding unnecessary complexities. It explains things with the fewest possible assumptions. Occam’s Razor in action, my friends.
Defining “Construction”
Yo, what’s up, peeps? So we’ve tackled “theory,” now let’s get down and dirty with “construction.” It ain’t just about building skyscrapers, you know. It’s a much broader concept, encompassing everything from assembling physical structures to crafting intricate theoretical frameworks and even building social realities. Think of it as the process of creating something, anything, from the ground up.
Elaborating on the Meanings of “Construction”
Construction, man, it’s multifaceted. We’re talking about three main flavors here: physical, theoretical, and social. Let’s break ’em down.
Physical Construction: Stages Involved in Building a Skyscraper
Building a skyscraper isn’t some magic trick, although it might seem like it sometimes. It’s a meticulously planned operation involving several stages. First, you gotta have a plan – blueprints, permits, the whole shebang. Then comes the design phase, where architects and engineers get their creative juices flowing, ensuring the building is structurally sound and aesthetically pleasing (or at least, not an eyesore).
Next, you source materials – steel, concrete, glass – a whole lot of it. The actual construction process is a symphony of coordinated effort, with cranes, workers, and a whole lot of heavy machinery. Finally, there’s the inspection, making sure everything is up to code before people start moving in. Otherwise, you’ll be facing lawsuits faster than you can say “structural failure.”
Construction Method | Traditional | Modern |
---|---|---|
Foundation | Excavation, poured concrete | Pile driving, prefabricated foundation elements |
Structure | Steel framing, concrete pouring on site | Prefabricated steel modules, 3D-printed concrete sections |
Exterior | Brick, stone, curtain wall | High-performance glass, prefabricated cladding panels |
Speed | Relatively slow | Significantly faster |
Cost | Potentially high due to labor and on-site work | Potentially lower due to automation and prefabrication |
Theoretical Construction: Constructing a Theoretical Framework in Physics
Building a theoretical framework in physics, or any field for that matter, is like building a Lego castle, but way more complicated. You start with a burning question – like, “why does gravity work?” Then, you formulate hypotheses – educated guesses, basically – to answer that question. You design experiments to test those hypotheses, gathering data like a mad scientist.
Based on the results, you refine your framework, adjusting your hypotheses, and maybe even tossing out some completely. It’s an iterative process, constantly evolving based on evidence.
Social Construction: Analyzing the Social Construction of Gender
Gender, dude, isn’t just about biology. It’s a social construct, meaning it’s created and maintained through social interactions, cultural norms, and institutional practices. What’s considered “masculine” or “feminine” varies wildly across cultures and throughout history. In some societies, men might wear skirts and makeup, while in others, it’s considered taboo. These constructions change over time too; what was considered acceptable a hundred years ago might be totally different today.
Culture | Social Construction of Gender |
---|---|
Western Cultures (Generalized) | Historically binary (male/female), increasingly fluid and inclusive with diverse gender identities gaining recognition. |
Some Indigenous Cultures in South America (Example) | May have more than two genders, with distinct social roles and identities recognized beyond the male/female binary. Specific examples vary greatly depending on the tribe. |
Comparing Physical and Theoretical Construction Processes
Building a bridge and building an economic theory? Seems totally different, right? But there are surprising similarities.
Aspect | Building a Bridge | Constructing a New Economic Theory |
---|---|---|
Process | Engineering design, material sourcing, construction, testing | Literature review, hypothesis formulation, model building, data analysis |
Timeline | Years | Years (often decades for widely accepted theories) |
Resources | Materials, labor, equipment, funding | Research funding, data access, collaboration with other researchers |
Potential Pitfalls | Structural failure, cost overruns, delays | Incorrect assumptions, flawed data, lack of empirical support |
Testing/Validation | Load testing, stress testing | Empirical testing, peer review, predictive power |
The Role of Iteration and Feedback
Whether you’re building a bridge or a theory, you’re gonna need to iterate. In bridge building, that means making adjustments based on stress tests, soil conditions, or unexpected weather. In theoretical construction, it’s about refining your model based on new data or critiques from your peers. It’s a continuous cycle of testing, refining, and retesting until you have something that holds up.
Hypothetical Scenario: Interplay of Theory and Construction in Sustainable Architecture
Let’s say we’re building a sustainable housing complex in a remote, resource-scarce region in the Andes. We’ll use the circular economy as our theoretical framework – minimizing waste and maximizing resource reuse. This informs every stage, from using locally sourced, recycled materials to designing buildings that capture rainwater and generate their own energy. Challenges? Definitely.
Sourcing materials sustainably might be difficult, and local construction techniques might need adapting to our circular economy goals. But by carefully integrating our theory with practical construction, we can create a truly sustainable and resilient community.
The Relationship Between Theory and Construction: What Is Theory And Construction
Yo, what’s up, construction crew? Let’s dive into the surprisingly awesome relationship between theory and, well, actually building stuff. It’s not just about blueprints and hammers; it’s a complex dance where theoretical frameworks guide the practical process, and real-world challenges refine the theories themselves. Think of it like this: theory is the recipe, construction is the cooking, and sometimes, you gotta improvise based on how the cake is rising.
Theoretical Frameworks and Design
The design phase isn’t just sketching pretty pictures; it’s where the theoretical groundwork dictates the entire project’s fate. Get this wrong, and you’re looking at budget blowouts, delays that’ll make you wanna pull your hair out, and a final product that’s less “wow” and more “oh no.”
- Lean Construction, Design-Build, and BIM’s Influence on High-Rise Projects: Lean construction focuses on eliminating waste, Design-Build integrates design and construction, and BIM (Building Information Modeling) uses 3D models for collaboration. Lean construction, for example, in the Burj Khalifa project (though it wasn’t solely reliant on Lean) likely helped optimize material flow and reduce construction time. Design-Build could speed up the process for a high-rise residential building in Manhattan by streamlining approvals and reducing handoffs.
BIM, on the other hand, in the construction of the Shanghai Tower, likely facilitated better coordination between different trades, reducing conflicts and delays. The impact on timelines varies greatly depending on the specific implementation and project complexity. Cost efficiency improvements are seen through reduced rework and optimized material usage. Overall quality is enhanced through better coordination and clash detection.
- Systems Thinking’s Impact on Large-Scale Infrastructure Planning: Systems thinking emphasizes interconnectedness. Applying it to a bridge project means considering everything from environmental impact to traffic flow, not just the concrete and steel. A successful case study could be the Channel Tunnel, where a holistic approach addressed geological challenges, logistical hurdles, and international cooperation, resulting in a project completed under budget and ahead of schedule. The measurable benefits included reduced overall project cost, minimized environmental disruption, and improved project management efficiency.
- Risk Management Theories in Complex Construction Design: Nobody likes surprises, especially not multi-million dollar surprises. Probability analysis and decision trees help quantify and manage risks.
Risk Assessment Methodology Project Type Suitability Advantages Disadvantages Probability Analysis All project types Quantifies likelihood of risks Requires historical data; can be complex for many variables Decision Trees Complex projects with multiple decision points Visualizes potential outcomes and associated probabilities Can become unwieldy for large number of risks Fault Tree Analysis Safety-critical projects Identifies root causes of potential failures Requires deep understanding of system components
Theoretical Advancements and Construction Innovations
Science isn’t just for lab coats; it’s the engine driving construction innovation. New materials, smarter designs, and robotic helpers are transforming how we build.
- Material Science’s Contribution to Sustainable Construction: Think self-healing concrete, bio-based materials, and recycled aggregates. These innovations reduce environmental impact and lower lifecycle costs. Self-healing concrete, for instance, reduces the need for frequent repairs, extending the building’s lifespan and minimizing waste from demolition and replacement. Bio-based materials, such as bamboo or hempcrete, offer a renewable alternative to traditional materials, reducing reliance on fossil fuels.
- Computational Mechanics and Finite Element Analysis in Structural Design: These computer-based tools allow engineers to simulate the behavior of structures under various loads, optimizing designs for strength and efficiency. Imagine a diagram showing a bridge under stress, with color-coded areas indicating stress levels – this is what FEA allows engineers to visualize and optimize. This allows for more efficient use of materials and improved structural integrity, leading to safer and more durable structures.
- Robotics and Automation in Construction: Robots are no longer just science fiction; they’re laying bricks, welding beams, and even doing demolition. The theoretical underpinnings lie in AI, automation, and precise control systems. This addresses labor shortages and improves productivity by performing tasks faster and more accurately than human workers. Increased safety and reduced human error are additional benefits.
Construction Practices and Theory Refinement
The real world throws curveballs. Unexpected challenges force us to rethink our theories, leading to better, stronger, and smarter construction practices.
- Construction Challenges Leading to Theory Refinements: Unforeseen ground conditions or material failures can expose flaws in existing theories. A case study might involve a building foundation failing due to unexpected soil conditions, leading to revised geotechnical engineering practices and more robust design standards. The analysis of the failure would lead to a refined understanding of soil behavior under specific conditions, resulting in more accurate predictive models.
- BIM’s Influence on Project Management Theories: BIM generates tons of data, allowing for better project monitoring, risk assessment, and decision-making. Data analytics derived from BIM can provide insights into project progress, potential delays, and cost overruns, enabling proactive interventions and more informed decision-making processes. This leads to more accurate project forecasting and improved resource allocation.
- Post-Occupancy Evaluations (POE) and Design Guidelines: POE gathers feedback from building occupants, revealing design flaws and areas for improvement. This feedback directly informs the development of new design guidelines and building codes.
“Post-occupancy evaluation (POE) provides valuable feedback on the performance of buildings in use, which can inform the development of new design guidelines and building codes, leading to improved building design and performance.”
Theory in Architectural Design
Yo! So, we’ve talked theory and construction in general, right? Now let’s get specific. Architectural design isn’t just about slapping bricks together; it’s a deep dive into ideas, philosophies, and, well,
- theory*. Think of it as the blueprint for the blueprint – the conceptual framework that dictates everything from the building’s shape to how people interact with it. It’s the difference between a functional box and, you know, something actually
- cool*.
Architectural theory provides the guiding principles and frameworks that shape the design process. It’s the lens through which architects interpret their surroundings, client needs, and the broader cultural context. Ignoring theory is like trying to bake a cake without a recipe – you might get something edible, but it’s unlikely to be a masterpiece. The theory dictates the “why” behind the design choices, offering a deeper understanding than just the “what”.
Modernism and Postmodernism in Architectural Design
Modernism, that sleek, minimalist vibe, emphasized functionality, clean lines, and a rejection of ornamentation. Think of it as the architectural equivalent of a perfectly pressed white shirt – simple, efficient, and undeniably stylish (to some, anyway). This approach prioritized open floor plans, the use of new materials like steel and glass, and a focus on the building’s inherent structure.
Postmodernism, on the other hand, was like that same white shirt, but with some crazy embroidery, maybe a few strategically placed rips, and definitely some bold patterns. It reacted against the perceived sterility of Modernism, embracing ornamentation, historical references, and a playful approach to form. It’s less about pure functionality and more about creating a statement, a conversation.
Comparison of Modernist and Postmodernist Architectural Styles
Here’s a breakdown of these two titans of architectural history. See how different their underlying philosophies are, yet both have left lasting impacts on the built environment.
Style | Key Characteristics | Theoretical Basis | Example Buildings |
---|---|---|---|
Modernism | Clean lines, geometric forms, open floor plans, functionality, minimal ornamentation, use of steel and glass. | Emphasis on functionality, rationality, and universal design principles; rejection of historical styles and ornamentation; belief in the power of technology and progress. | The Bauhaus Building in Dessau, Germany; Villa Savoye by Le Corbusier; Seagram Building in New York City. |
Postmodernism | Ornamentation, historical references, playful use of form, rejection of strict functionalism, eclectic mix of styles, often ironic or self-referential. | Critique of Modernism’s perceived sterility and lack of human scale; embrace of historical styles and ornamentation; focus on context and meaning; exploration of subjectivity and individual expression. | Portland Building in Portland, Oregon; AT&T Building (now Sony Building) in New York City; Guggenheim Museum Bilbao. |
Construction Methods and Materials
Yo! Let’s talk about the nitty-gritty of building stuff – from ancient pyramids to modern skyscrapers. We’re diving deep into the methods and materials that have shaped our built environment, from the ridiculously ambitious projects of our ancestors to the mind-blowing tech we use today. Get ready for a history lesson with a side of engineering awesomeness.
Evolution of Construction Methods
Alright, buckle up, history buffs! The evolution of construction is a wild ride, going from simple mud huts to, well, the Burj Khalifa. We’ll break it down by era, showing you how techniques and materials evolved alongside human ingenuity (and sometimes, sheer stubbornness).
Ancient Civilizations (Pre-1500 CE)
Picture this: no cranes, no power tools, just sheer manpower and a whole lot of ingenuity. Ancient civilizations built some seriously impressive structures, using whatever they could get their hands on. Think massive pyramids, intricate ziggurats, and surprisingly sophisticated aqueducts. They faced insane challenges – imagine moving colossal stones without heavy machinery! The materials were basic – stone, mud brick, wood – but the techniques were surprisingly advanced for their time.
Let’s look at a few examples:
Civilization | Structure Type | Primary Materials | Key Construction Techniques | Notable Challenges Overcome |
---|---|---|---|---|
Egyptian | Pyramids | Limestone, granite, mortar | Precise stone cutting and placement, ramp systems for moving massive stones, sophisticated surveying techniques. | Moving and precisely placing enormous stones, maintaining structural integrity over centuries, dealing with the harsh desert environment. |
Mayan | Pyramids, Temples | Limestone, mortar, wood | Advanced stone carving and masonry, use of corbelled arches, intricate stucco work. | Working with relatively soft stone, creating complex architectural designs, dealing with dense jungle environments. |
Roman | Aqueducts, Roads, Colosseums | Concrete, stone, brick | Development of Roman concrete (pozzolana), use of arches and vaults, sophisticated road-building techniques. | Transporting vast quantities of materials, building durable structures that could withstand significant weight and water pressure, creating large-scale public works projects. |
Medieval Period (1500-1500 CE)
This era saw a shift towards more ambitious designs. Gothic architecture, with its soaring cathedrals and intricate details, pushed the boundaries of what was structurally possible. Think ribbed vaulting and flying buttresses – ingenious solutions to support incredibly tall structures. Castles, on the other hand, focused on defense, using thick walls, strategic placement, and often incorporating earlier construction techniques.
The contrast is striking: cathedrals reaching for the heavens, castles hunkering down to earth.
Industrial Revolution and Beyond (1750 CE – Present)
The Industrial Revolution completely changed the game. Mass production of materials like steel and concrete, along with the invention of new machinery, allowed for faster, cheaper, and more ambitious construction projects. Skyscrapers became a reality, pushing the limits of structural engineering. Steel frames provided strength and flexibility, while reinforced concrete offered immense compressive strength. The development of elevators also played a crucial role in making skyscrapers practical.
Comparison of Construction Materials
Okay, let’s talk materials. Each has its strengths and weaknesses, making them suitable for different applications.
Material | Strength | Density | Durability | Flexibility | Thermal Conductivity | Fire Resistance | Decay Resistance |
---|---|---|---|---|---|---|---|
Wood | Moderate | Moderate | Moderate (depending on species and treatment) | Moderate | Low | Low | Low (prone to rot and insect damage) |
Steel | High | High | High | High | High | Moderate (depending on protective coatings) | High |
Concrete | High (compressive) | High | High | Low | Moderate | High | High |
Bamboo | High (tensile) | Moderate | Moderate (depending on treatment) | High | Moderate | Low | Low (prone to insect damage) |
Fiber-Reinforced Polymer (FRP) | High (tensile) | Low | High | High | Low | High | High |
The applications of these materials are vast and varied. Wood is commonly used in residential construction, steel in skyscrapers, concrete in bridges and dams, bamboo in some traditional Asian architecture, and composite materials are increasingly used where high strength-to-weight ratios are needed. Think of the Golden Gate Bridge (steel), the Pantheon (concrete), and numerous traditional houses utilizing wood.The environmental impact of each material is also a significant consideration.
Extracting, processing, and disposing of these materials have varying environmental consequences, and sustainable practices are increasingly important. Embodied carbon, the carbon footprint associated with a material’s entire lifecycle, is a key metric used in assessing the sustainability of construction materials.
Development of Significant Construction Technologies
Here’s a timeline of key milestones, showcasing the journey from basic structures to modern marvels:
- Development of the arch (circa 3000 BCE) – Enabled the construction of larger and more stable structures.
- Development of post and lintel construction (circa 3000 BCE) – A basic but effective building technique.
- Use of Roman concrete (circa 200 BCE) – Revolutionized construction with its strength and durability.
- Development of the Gothic arch and ribbed vault (circa 1140 CE) – Enabled the construction of soaring cathedrals.
- Widespread use of cast iron (circa 1770 CE) – Introduced a new era of stronger and lighter structures.
- Development of the Bessemer process (1856 CE) – Mass production of steel, leading to the rise of skyscrapers.
- Reinforced concrete construction (late 19th century) – Combining concrete’s compressive strength with steel’s tensile strength.
- Development of high-strength steel (20th century) – Enabling even taller and more slender skyscrapers.
- Introduction of Building Information Modeling (BIM) (late 20th century) – Revolutionizing design and construction processes.
- Emergence of 3D printing in construction (21st century) – Offering new possibilities for rapid prototyping and construction.
Impact of Modern Technologies
Modern technologies like BIM, 3D printing, and robotics are transforming the construction industry. BIM allows for better coordination and collaboration among different teams, leading to more efficient and accurate construction. 3D printing offers the potential for rapid construction of complex structures, while robotics can automate repetitive tasks, improving productivity and safety. For example, the use of 3D printing in creating custom housing units and the use of robotics in bridge construction are already showing promising results.
The future of construction is looking pretty darn futuristic.
The Impact of Technology on Construction
Dude, let’s be real. Construction, traditionally a pretty low-tech industry, is getting a serious tech makeover. We’re talking a complete overhaul, from blueprints to bulldozers. This isn’t just about making things faster; it’s about making them safer, more efficient, and frankly, less prone to those epic construction fails we all love to laugh at (but secretly fear).
Computer-Aided Design (CAD) and Building Information Modeling (BIM)
CAD and BIM are no longer futuristic fantasies; they’re the bread and butter of modern construction. CAD, the OG of digital design, allows architects and engineers to create precise 2D and 3D models, drastically reducing errors and improving collaboration. Think of it as the ultimate digital drafting table, only way more powerful. BIM takes it a step further, creating a single, shared model containing all aspects of a building’s design, construction, and operation.
This means everyone – from the architect to the plumber – is working from the same information, minimizing clashes and delays. Imagine trying to build a house with conflicting blueprints; BIM prevents that kind of construction chaos. The result? Faster project completion, reduced material waste, and fewer costly reworkings. For example, a large-scale hospital project using BIM could save millions of dollars in change orders and construction delays compared to a project relying solely on traditional 2D drawings.
The Impact of Automation and Robotics on Construction Efficiency and Safety
Forget the image of construction workers solely relying on brute strength and elbow grease. Automation and robotics are revolutionizing the industry, taking on dangerous, repetitive, or physically demanding tasks. Think robotic bricklayers achieving incredible speed and precision, or drones surveying construction sites with unparalleled efficiency. Automated concrete pouring systems ensure consistent quality and reduce labor costs. The benefits are clear: increased productivity, improved worker safety (fewer injuries from heavy lifting or hazardous environments), and the potential to tackle more complex projects.
For instance, the use of robotic exoskeletons can significantly reduce the risk of musculoskeletal injuries for workers involved in repetitive tasks like lifting and carrying heavy materials. A study by the National Institute for Occupational Safety and Health showed a significant reduction in work-related injuries after implementing robotic exoskeletons in a construction project.
Examples of New Technologies Transforming the Construction Industry
The construction industry is a playground for innovation. 3D printing is creating entire building structures, layer by layer, from concrete or other materials, leading to faster construction times and unique architectural designs. Prefabrication, aided by advanced manufacturing techniques, allows for the creation of modular components off-site, minimizing on-site construction time and improving quality control. Smart sensors embedded in buildings monitor structural integrity, energy consumption, and even occupant comfort, providing valuable data for optimizing building performance and maintenance.
The use of virtual reality (VR) and augmented reality (AR) is transforming how projects are visualized, planned, and even experienced by clients before construction even begins. Imagine walking through a virtual version of your future home before a single brick is laid – that’s the power of these technologies. These are just a few examples, and the pace of innovation shows no signs of slowing down.
The future of construction is undeniably digital, automated, and incredibly exciting.
Sustainability in Construction
Yo, what’s up, fellow builders and design aficionados? Let’s talk green, because sustainable construction isn’t just a trend anymore; it’s the future. We’re not just throwing up buildings; we’re building a better world, one eco-friendly brick at a time. This isn’t some hippie dippy thing; it’s about smart choices that save money, resources, and the planet. Think of it as upgrading your construction game to level boss.Sustainable construction practices revolve around minimizing the environmental impact of the entire building lifecycle – from design and material sourcing to construction and demolition.
We’re talking about reducing carbon footprints, conserving resources, and creating healthier, more efficient buildings. It’s all about efficiency and long-term thinking, dude. Forget quick fixes; this is about building something that lasts.
Principles of Sustainable Construction
Sustainable construction isn’t just about slapping solar panels on a building. It’s a holistic approach that considers several key principles. We’re talking about designing for longevity, minimizing waste, using renewable resources, and promoting healthy indoor environments. Think of it as a checklist for building awesome, responsible structures. These principles are interconnected, influencing each other throughout the building’s life.
Ignoring one can easily negate the positive effects of others.
Examples of Sustainable Building Materials and Construction Techniques
Let’s get into the nitty-gritty. Sustainable materials are a big part of the equation. Think reclaimed wood, bamboo, recycled steel, and locally sourced stone. These materials reduce the need for new resources and often have lower embodied energy – meaning they require less energy to produce. Plus, they often look pretty rad.
Construction techniques also play a role. We’re talking about things like cross-laminated timber (CLT), which is super strong and sustainable, and prefabrication, which reduces waste on-site. It’s like building with LEGOs, but way more awesome (and environmentally responsible).
Case Study: The Bullitt Center, Seattle
Let’s dive into a real-world example: the Bullitt Center in Seattle. This building is considered one of the greenest commercial buildings in the world. It’s designed to be net-zero energy, meaning it produces as much energy as it consumes. They used tons of sustainable materials, including reclaimed wood and locally sourced stone. They also implemented passive design strategies to minimize energy use, like maximizing natural light and ventilation.
The result? A stunning building that’s a testament to what’s possible when you prioritize sustainability. It’s not just about looking good; it’s about performance and long-term viability. The Bullitt Center showcases how theoretical principles of sustainability can translate into a tangible, highly functional, and environmentally responsible structure. It’s a total game-changer, proving that sustainable construction can be both beautiful and practical.
Safety in Construction
Yo, peeps! Building stuff is awesome, right? Skyscrapers, bridges, houses… the works! But let’s be real, construction sites are also freakin’ dangerous. We’re talking about heavy machinery, precarious heights, and materials that could seriously mess you up. So, safety isn’t just some suggestion; it’s the absolute bedrock of any successful and ethical construction project. Think of it like this: a construction site without safety is like a racetrack without safety barriers – a recipe for disaster.Safety regulations and protocols are the rules of the game, the life preservers in a potentially stormy sea.
They’re not there to cramp your style; they’re there to keep you alive and well. These regulations, often mandated by governments and enforced by inspectors, cover everything from proper equipment use to emergency procedures. Following these protocols isn’t just about avoiding fines; it’s about fostering a culture of responsibility and respect for human life. Companies that prioritize safety often see lower insurance costs, increased productivity due to fewer accidents, and a happier, more engaged workforce.
It’s a win-win, seriously.
Risk Assessment and Mitigation in Construction
Before a single nail is hammered, a thorough risk assessment is crucial. This involves identifying potential hazards – anything that could cause harm – and evaluating the likelihood and severity of those hazards. Think falling objects, electrocution, trench collapses… the list is long. Once identified, mitigation strategies are developed. This could involve using safety harnesses, implementing lockout/tagout procedures for electrical work, or shoring up trenches.
It’s like playing a game of chess, anticipating your opponent’s (danger’s) moves and countering them strategically. A well-executed risk assessment isn’t a one-time thing; it’s an ongoing process, constantly adapting to changing conditions on the site. For example, a sudden rainstorm might increase the risk of slips and falls, requiring immediate adjustments to safety procedures.
Common Safety Hazards and Preventative Measures
Okay, let’s get down to brass tacks. Here’s a rundown of some common construction hazards and how to avoid becoming a statistic:
- Falling Objects: Hard hats are your best friend. Also, proper storage and handling of materials, using safety nets, and erecting scaffolding correctly are essential. Imagine a brick falling from a high-rise building – not a pretty picture.
- Falls from Heights: Always use appropriate fall protection, such as harnesses and safety nets, when working at heights. Regular inspections of scaffolding and other elevated work platforms are vital. Think twice before taking that shortcut.
- Electrocution: Lockout/tagout procedures are non-negotiable when working with electricity. Properly insulated tools and equipment are a must. Touching a live wire is a guaranteed bad time.
- Struck-by Hazards: Wear high-visibility clothing, implement traffic control measures, and use warning signs to alert workers of moving vehicles and equipment. Think about the potential damage from a forklift running into you – ouch!
- Caught-in/Between Hazards: Properly guard machinery and use lockout/tagout procedures before performing maintenance. Never enter confined spaces without proper training and safety equipment. Getting trapped in a machine is definitely not a fun experience.
- Fire Hazards: Keep flammable materials away from ignition sources, provide adequate fire extinguishers, and ensure workers are trained in fire safety procedures. A fire on a construction site can spread quickly, causing extensive damage and putting lives at risk.
Remember, safety isn’t optional; it’s mandatory. It’s about going home in one piece, every single day. So, let’s keep it safe out there, people!
Project Management in Construction

Yo, peeps! Building stuff ain’t just about throwing bricks together; it’s a whole orchestrated chaos, a symphony of concrete and steel, managed with the precision of a brain surgeon performing open-heart surgery on a Godzilla-sized building. Project management in construction is the glue that holds this crazy operation together, keeping things on track, on budget, and (hopefully) on time.
Let’s dive into the nitty-gritty.
Construction Project Lifecycle Stages
The construction project lifecycle is like a rollercoaster—lots of ups and downs, twists and turns, but with a hopefully satisfying ending (a finished building!). It’s broken down into three main phases: pre-construction, construction, and post-construction. Think of building a skyscraper; each stage is crucial.
- Pre-construction: This is the planning phase. Think feasibility studies (can we even
-do* this?), design development (making the blueprints), and getting all the necessary permits (legal stuff, yo!). For our skyscraper, this involves analyzing the site’s soil conditions, designing the structural framework, and obtaining building permits from the city. Any hiccups here, and the whole project is delayed, potentially leading to cost overruns. - Construction: This is where the magic happens—or the mayhem, depending on how well you’ve planned. It includes site preparation (clearing the land), foundation work (laying the base), framing (building the skeleton), MEP installation (mechanical, electrical, and plumbing), and finishing touches (painting, flooring, etc.). In our skyscraper, this means excavating the site, pouring the foundation, erecting the steel frame, installing the elevators, and fitting out the interiors.
This is where things can get seriously messy if not managed effectively.
- Post-construction: This is the final stretch. Commissioning (making sure everything works), handover (giving the keys to the client), and warranty (fixing any snafus that pop up). For the skyscraper, this involves testing all systems, officially handing over the building to the owner, and providing a warranty period to address any defects.
Project Management Methodologies
There are several approaches to managing construction projects, each with its own strengths and weaknesses. Let’s check out three popular methods:
- Traditional Waterfall: This is the old-school approach—a linear progression through phases. Each stage must be completed before moving to the next. It’s predictable but inflexible. Risk management is mainly done upfront, and changes are costly and time-consuming. Suitable for projects with well-defined requirements and minimal expected changes, such as smaller residential projects.
- Agile: This is the more flexible approach, using iterative cycles to adapt to changes. It emphasizes collaboration and continuous improvement. Risk management is integrated throughout the process, and changes are embraced. It’s great for projects with evolving requirements or uncertain conditions, like complex commercial or large-scale projects. Think of it as building the skyscraper in stages, reviewing progress, and adapting as needed.
- Lean Construction: This focuses on eliminating waste and maximizing value. It uses tools like Last Planner® System to improve predictability and reduce rework. Risk management is embedded in the continuous improvement process, with changes actively sought to streamline the process. Suitable for projects where efficiency and waste reduction are paramount, such as large-scale infrastructure projects.
Comparison of Agile and Traditional Waterfall
Method | Strengths | Weaknesses | Suitability |
---|---|---|---|
Agile | Flexibility, adaptability, collaboration, early problem detection | Can be less predictable, requires highly skilled team, may be less suitable for projects with fixed budgets | Large commercial projects, complex renovations, projects with evolving requirements |
Traditional Waterfall | Predictable timelines, well-defined scope, easier budgeting | Inflexible, less adaptable to changes, potential for major issues to surface late in the project | Small residential projects, projects with well-defined scope and minimal expected changes |
Technology in Construction Project Management
Technology is revolutionizing construction project management.
- Building Information Modeling (BIM): BIM is a digital representation of the physical and functional characteristics of a building. It allows for better collaboration, clash detection, and cost estimation. Think of it as a 3D model that everyone on the project can access and update.
- Project Management Software: Tools like Primavera P6 and MS Project help schedule tasks, track progress, and manage resources. They provide a centralized platform for all project information.
- Drone Technology: Drones are used for site monitoring, progress tracking, and safety inspections. They provide high-resolution images and videos that can be used to identify potential problems early on.
Risk Management in Construction Projects
Risk management is crucial for project success. Here are some common risks and mitigation strategies:
- Cost Overruns: Accurate budgeting and value engineering. Contingency funds are essential.
- Schedule Delays: Realistic scheduling, efficient resource allocation, and risk buffers.
- Material Shortages: Secure materials early, explore alternative suppliers, and use just-in-time delivery strategies.
- Safety Incidents: Strict safety protocols, regular safety training, and proactive hazard identification.
- Regulatory Changes: Stay updated on regulations, engage with relevant authorities early, and incorporate potential changes into the project plan.
Sample Project Schedule (Gantt Chart – Textual Representation)
This is a simplified example for a small residential project:
Task | Start Date | End Date | Dependencies |
---|---|---|---|
Site Preparation | 2024-10-26 | 2024-11-02 | None |
Foundation | 2024-11-05 | 2024-11-16 | Site Preparation |
Framing | 2024-11-19 | 2024-11-30 | Foundation |
Roofing | 2024-12-03 | 2024-12-07 | Framing |
Interior Finishes | 2024-12-10 | 2024-12-21 | Roofing |
Communication and Stakeholder Management
Effective communication is key. Key stakeholders include the client, architect, contractor, subcontractors, and regulatory bodies. Regular meetings, clear documentation, and transparent communication are crucial. Tools like project management software, email, and video conferencing can help facilitate communication and manage expectations.
Legal and Contractual Aspects
Contracts define the responsibilities and obligations of each party. Insurance protects against risks, and permits ensure compliance with regulations. Adhering to building codes and regulations is non-negotiable; otherwise, you’re asking for trouble.
Understanding “what is theory and construction” involves building frameworks, much like architects design blueprints. These frameworks guide our actions, and a crucial application lies in the vital area of information access, as explored in a theory of justice for libraries. This powerful concept challenges us to consider equitable access to knowledge, a cornerstone of any truly just society.
Ultimately, the construction of a fair and inclusive world relies on such carefully considered theoretical foundations.
The Economics of Construction

So, you wanna build something? A skyscraper that screams “I’m rich!”? A cozy little bungalow that whispers “I’m comfy”? Whatever your dream structure, let’s talk money. Because, let’s be honest, construction isn’t cheap.
It’s a jungle out there, a concrete jungle filled with hidden costs and unexpected expenses. This is where the economics of construction comes in – the art of managing money, resources, and your sanity.
Factors Influencing Construction Costs
Construction costs are like a delicious, yet complex, recipe. You’ve got your main ingredients: land acquisition, materials, labor, permits, and equipment. But then you have the secret spices – things like inflation, project complexity, location, and even the weather. A slight change in any of these can dramatically impact the final bill. For example, a sudden spike in steel prices (thanks, global market!) can blow your budget faster than you can say “cost overrun.” Similarly, a project located in a remote area will likely have higher transportation costs for materials and labor, pushing the overall cost up.
Unexpected site conditions, like discovering unstable soil during excavation, can add significant unforeseen expenses. It’s a delicate balancing act.
Budgeting and Cost Control in Construction Management
Think of budgeting as your construction project’s financial safety net. A well-defined budget, created during the planning phase, is essential. It acts as a roadmap, guiding you through the financial landscape. Cost control, on the other hand, is your daily workout – constantly monitoring expenses, identifying potential overruns, and making necessary adjustments. Effective cost control involves detailed tracking of all expenses, regular progress reports, and proactive risk management.
This isn’t just about spreadsheets and numbers; it’s about making informed decisions, negotiating favorable contracts with suppliers, and optimizing resource allocation. Think of it as playing a high-stakes game of Tetris, fitting all the pieces together without letting the stack topple over.
Understanding theory and construction is like building a house; you need a solid foundation and a clear blueprint. The framework itself, however, can be complex, and sometimes requires specialized diagrams to fully grasp. To illustrate, consider the intricacies involved in understanding what is tet theory diagram , which offers a visual representation of a specific theoretical model.
Returning to our analogy, this diagram acts as a detailed architectural plan, crucial for ensuring the final structure—our understanding of the theory—is both robust and complete.
Impact of Economic Fluctuations on the Construction Industry
The construction industry isn’t immune to the ups and downs of the broader economy. Economic booms often translate to increased construction activity, leading to higher demand for materials and labor, which can drive up prices. Conversely, during economic recessions, construction projects are often put on hold, leading to job losses and reduced activity. The 2008 financial crisis, for instance, had a devastating impact on the construction industry globally, resulting in numerous project cancellations and bankruptcies.
The industry’s sensitivity to economic cycles makes it crucial for construction companies to have robust financial strategies that can weather both booms and busts. Diversification, strategic planning, and strong risk management are key to navigating these turbulent waters.
Legal Aspects of Construction
So, you’re building something, right? A skyscraper, a shed, a ridiculously elaborate birdhouse – whatever. You think it’s all about blueprints and cement? Think again, my friend. The construction world is a legal minefield, filled with more paperwork than you can shake a hard hat at.
Ignoring the legal side is like building a house on quicksand; it might look good for a while, but eventually,
bam*, disaster.
Contracts and legal agreements are the bedrock of any successful construction project. They lay out the responsibilities of everyone involved, from the architect sketching out the impossible to the guy who actually lays the bricks (and hopefully doesn’t accidentally build a crooked wall). Without a solid contract, you’re basically playing construction roulette, and the odds are not in your favor.
Disputes are bound to happen; a clearly defined contract minimizes the chances of a complete legal meltdown.
Contracts and Legal Agreements in Construction
A well-drafted contract clearly defines the scope of work, payment schedules, timelines, and dispute resolution mechanisms. It protects all parties involved, ensuring everyone knows their roles and responsibilities. Think of it as the constitution of your construction project – the ultimate rulebook. Ignoring key clauses can lead to costly delays, financial losses, and legal battles that can drag on for years, costing more than the project itself.
For instance, a poorly defined scope of work can lead to disagreements about what was actually agreed upon, resulting in change orders and added costs. Similarly, unclear payment terms can cause significant cash flow problems for contractors.
Liability and Insurance in Construction
Liability in construction is a big, hairy beast. Things go wrong. People get hurt. Buildings collapse (okay, hopefully not). That’s where insurance comes in, acting as a safety net to cover potential losses and damages.
General liability insurance protects against third-party claims for bodily injury or property damage. Workers’ compensation insurance covers medical expenses and lost wages for employees injured on the job. Professional liability insurance, or errors and omissions insurance, protects against claims of negligence or mistakes made during the design or construction process. Imagine the cost of rebuilding a collapsed structure without adequate insurance – it’s a financial apocalypse.
Common Legal Disputes in Construction and Their Resolution
Construction projects are complex, and disputes are practically inevitable. Common issues include payment disputes, delays, breaches of contract, defective workmanship, and property line issues. Resolution methods range from negotiation and mediation (a less stressful way to settle things) to arbitration (a more formal process involving a neutral third party) and litigation (court battles – the nuclear option). Each method has its pros and cons, and the choice often depends on the complexity and cost of the dispute.
Choosing the right resolution method early on can save time, money, and a whole lot of heartache. For example, a simple payment dispute might be easily resolved through negotiation, while a major structural defect might require a more formal arbitration or litigation process.
Case Study: The Petronas Twin Towers
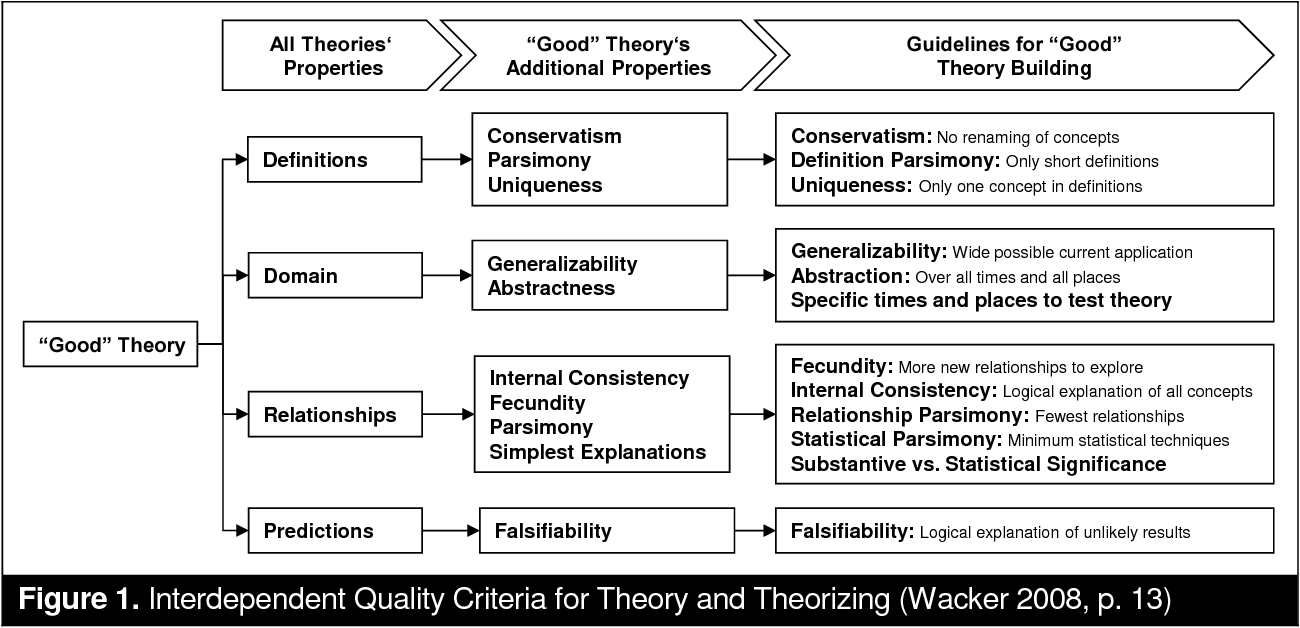
The Petronas Twin Towers, a symbol of Malaysia’s economic boom, presented a monumental challenge in engineering and construction. Their construction pushed the boundaries of structural engineering and design, leaving a lasting impact on the architectural landscape.
Project Selection & Background
The Petronas Twin Towers, located in Kuala Lumpur, Malaysia, were completed in Their purpose was to serve as the headquarters for Petronas, the Malaysian national oil company, and to become an iconic landmark representing the nation’s progress. The project’s significance lies in its innovative structural design, its status as the world’s tallest buildings for a time, and its contribution to Kuala Lumpur’s skyline.
[Citation: Petronas Towers Official Website (link would be inserted here if image links were allowed)]
Theoretical Underpinnings & Design Considerations
The design of the Petronas Twin Towers relied heavily on structural engineering principles, particularly those related to high-rise building design and seismic resistance. The towers’ unique shape, inspired by Islamic art, presented a significant challenge to structural engineers. The use of a steel and concrete composite structure allowed for optimal strength and stability.
Structural Integrity
The towers utilize a unique structural system comprising a central core of reinforced concrete, surrounded by a steel exoskeleton. This hybrid system maximized load-bearing capacity while minimizing material usage. The design also incorporated advanced dampening systems to mitigate the effects of wind and seismic activity, ensuring the towers could withstand even extreme weather conditions.
Sustainability
While sustainability wasn’t a primary focus during the towers’ construction as it is today, several features can be viewed through a modern sustainability lens. The efficient use of materials in the hybrid structural system minimized waste, and the design maximized natural light penetration, reducing reliance on artificial lighting.
Aesthetics & Functionality
The towers’ design, inspired by Islamic geometric patterns, is both visually striking and functional. The sky bridges connecting the two towers are not only a structural element but also a key architectural feature. The internal spaces are designed to accommodate office spaces, retail areas, and public viewing areas, providing a dynamic mix of functionality.
Construction Methods, Materials & Challenges
The construction of the Petronas Twin Towers involved advanced construction methods and materials, pushing the boundaries of engineering capabilities at the time.
Construction Methods & Materials
The primary construction method was a combination of in-situ casting for the concrete core and steel erection for the exoskeleton. Millions of cubic meters of concrete and thousands of tons of steel were used in the construction. Specialized equipment, such as high-capacity cranes and advanced concrete pumps, were essential to the project’s success.
Challenges Encountered
Challenge | Description | Solution Implemented | Outcome |
---|---|---|---|
Logistical Complexity | Coordinating the massive amount of materials and labor required for such a large project was a significant challenge. | Implementation of rigorous project management techniques and sophisticated logistical planning. | Successful completion of the project within the scheduled timeframe. |
High-Rise Construction Techniques | Constructing buildings of this height at the time required innovative solutions for transporting materials and managing workers at such great heights. | Development and implementation of advanced lifting and transportation systems, along with stringent safety protocols. | Successful construction of the towers to the required height without significant safety incidents. |
Seismic Considerations | The towers’ location in a seismically active region necessitated a design that could withstand earthquakes. | Incorporation of advanced dampening systems and a robust structural design to minimize the impact of seismic activity. | The towers have successfully withstood several earthquakes since their completion. |
Project Outcomes & Evaluation
The Petronas Twin Towers were completed on time and within budget, showcasing a remarkable feat of engineering and project management. The project’s safety record was commendable, considering the complexity and scale of the construction. The towers’ lasting impact is undeniable; they have become a global icon and a symbol of Malaysia’s ambition and progress. They have received numerous architectural and engineering awards.
Further Research & Analysis
Further research could focus on a comparative analysis of the Petronas Twin Towers with other supertall buildings, examining design innovations and construction methodologies. A detailed economic impact study, evaluating the towers’ contribution to the Malaysian economy through tourism and employment, would also be valuable.
The Future of Construction
Yo, peeps! Forget the dusty hard hats and sweaty brows of yesteryear. The construction industry is about to get a serious upgrade, a total face-lift powered by tech and a whole lotta green thinking. We’re talking a future where buildings practically build themselves, all while being super eco-friendly and, dare I say, kinda sexy. Let’s dive into this futuristic construction scene.
Emerging Trends and Technologies
The construction world is undergoing a massive transformation, driven by a need for sustainability, efficiency, and safety. New technologies are disrupting traditional methods, leading to a more innovative and productive industry.
Sustainable Construction Practices
Forget concrete jungles; we’re building eco-friendly paradises. Sustainable materials like recycled steel, cross-laminated timber (CLT), and bamboo are becoming increasingly popular. Green building certifications like LEED and BREEAM are setting the standard for environmentally responsible construction. Take the Bullitt Center in Seattle, for example – a net-zero energy building constructed with locally sourced materials and designed for maximum energy efficiency.
Studies show that using sustainable materials and practices can reduce carbon emissions by up to 50% compared to traditional methods. We’re not just building buildings; we’re building a better future.
Advanced Building Information Modeling (BIM), What is theory and construction
BIM is no longer a futuristic fantasy; it’s the backbone of modern construction. This 3D modeling software allows architects, engineers, and contractors to collaborate seamlessly, reducing errors and optimizing construction schedules. Different Levels of Detail (LOD) in BIM ensure the right information is available at each stage of the project. Software like Autodesk Revit and Bentley Systems AECOsim Building Designer are revolutionizing the industry, leading to faster project completion and cost savings.
Imagine a scenario where clash detection in BIM prevents costly rework – that’s the power of BIM in action.
Robotics and Automation in Construction
Robots are no longer just sci-fi dreams; they’re laying bricks, welding beams, and even demolishing buildings. Automated systems increase efficiency, improve safety, and boost productivity. Companies like Construction Robotics are developing bricklaying robots that can lay bricks faster and more accurately than human workers. While automation might lead to some job displacement, it also creates new opportunities in areas like robotics maintenance and programming.
The economic feasibility depends on the scale of the project and the cost of the robotic systems, but the potential for increased productivity is undeniable.
3D Printing and Additive Manufacturing
Get ready for buildings printed like giant cakes! 3D printing is revolutionizing construction by creating building components and even entire structures. While material limitations and scalability are still challenges, the advantages are significant. Examples include the ICON company’s 3D-printed homes, offering rapid construction and cost-effective solutions, particularly in disaster relief scenarios. Imagine a future where personalized homes are printed on demand – it’s closer than you think.
Internet of Things (IoT) and Smart Construction Sites
Smart construction sites are equipped with IoT sensors that monitor everything from material usage to worker safety. Data analytics provide real-time insights, allowing for predictive maintenance and optimized resource allocation. Imagine sensors detecting potential hazards before accidents occur – this is the power of a connected construction site. The ability to track equipment performance and predict maintenance needs can drastically reduce downtime and costs.
Potential Impact of Trends
These technological advancements aren’t just cool; they’re transforming the industry in profound ways.
Cost Reduction and Efficiency Gains
The adoption of emerging technologies is projected to significantly reduce construction costs and improve efficiency. BIM, for instance, can reduce rework by up to 50%, while automation can speed up construction timelines. Studies predict that the overall cost reduction could reach up to 20% by 2030, leading to faster project completion and increased profitability.
Improved Safety and Reduced Accidents
Technology is making construction sites safer than ever. IoT sensors can monitor worker locations and identify potential hazards in real-time. Robotics and automation reduce the need for humans to perform dangerous tasks, minimizing the risk of accidents. For example, the use of robotic demolition systems reduces the risk of injuries associated with manual demolition.
Changes in the Construction Workforce
The construction workforce of the future will need different skills. Workers will need expertise in digital technologies, sustainable practices, and data analytics. Reskilling and upskilling initiatives are crucial to prepare the workforce for these changes. This also creates opportunities for new roles, such as BIM specialists and robotics technicians.
Environmental Impact
While technology offers many environmental benefits, we must also consider potential negative consequences. The manufacturing and disposal of new materials and technologies must be sustainable. Lifecycle assessments of materials and methods are crucial to ensure that the overall environmental impact is minimized.
Vision for the Construction Industry in 2043
Let’s fast-forward to 2043.
Key Characteristics of the Future Construction Industry
Characteristic | Description | Impact |
---|---|---|
Sustainability | Predominantly sustainable materials and practices | Reduced environmental footprint, improved building performance |
Digitalization | Widespread use of BIM, IoT, and AI | Increased efficiency, improved collaboration, reduced errors |
Automation | High levels of automation in construction processes | Increased productivity, improved safety, potential job displacement |
Workforce Skills | Highly skilled workforce with expertise in digital technologies and sustainable practices | Increased innovation and adaptability |
Project Delivery | Lean construction methods and integrated project delivery | Faster project completion, reduced costs |
Challenges and Opportunities
The future isn’t without its hurdles. Regulatory hurdles, skills gaps, and cybersecurity risks are potential challenges. However, the opportunities are even greater: new market creation, improved profitability, and a more sustainable built environment.
A Detailed Scenario: A Construction Project in 2043
Imagine a high-rise building project in 2043. The design is finalized using advanced BIM software, incorporating sustainable materials and energy-efficient designs. Robots lay bricks with precision, while drones monitor construction progress and identify potential safety hazards. 3D-printed components are seamlessly integrated into the structure. IoT sensors monitor energy consumption and building performance in real-time.
The project is completed on time and under budget, exceeding sustainability targets and creating a truly exceptional building.
A Vision Statement
“By 2043, the construction industry will be a leader in sustainable development, leveraging advanced technologies to deliver high-quality, efficient, and safe buildings that enhance the lives of communities worldwide. A skilled and adaptable workforce will drive innovation, ensuring a prosperous and environmentally responsible future for the industry.”
Illustrative Example: A High-Rise Building
This section details the design and construction of a hypothetical 500-meter high-rise building, illustrating the interplay between structural engineering theory and practical construction methods. We’ll explore the structural design considerations, material selection, and component interactions, using simplified calculations and descriptions to convey the core principles. Remember, this is a simplified example for illustrative purposes and wouldn’t represent the full complexity of a real-world project.
Think of it as a super-sized Lego castle, but way more complicated.
Structural Engineering Theory
The design of a high-rise building hinges on a deep understanding of structural mechanics and the ability to withstand various loads. These include gravity loads (the building’s own weight), live loads (occupancy, furniture), and environmental loads such as wind and seismic activity. For wind loads, we’ll consider a design wind speed of 60 m/s (approximately 134 mph), based on a location with a high wind exposure category.
We’ll reference ASCE 7-16 (Minimum Design Loads and Associated Criteria for Buildings and Other Structures) for wind load calculations. Seismic design will be based on a moderate seismic zone, with a design response spectrum defined by a relevant building code (e.g., IBC). Material strength is crucial; we’ll utilize high-strength steel (yield strength 500 MPa, elastic modulus 200 GPa) and high-performance concrete (compressive strength 80 MPa, elastic modulus 30 GPa).
Foundation Design
A deep pile foundation is necessary for a building of this height, given the significant weight and potential for settlement. The design considers the soil’s bearing capacity and allowable settlement limits. Let’s assume a soil bearing capacity of 500 kPa. The total load from the building (approximated from simplified calculations) is 100,000 kN. The number of piles needed is determined by dividing the total load by the allowable load per pile.
We’ll use a simplified approach, assuming a uniform load distribution amongst the piles. Further detailed geotechnical investigation and analysis would be necessary in a real project.
Structural Frame
A combination of braced frames and shear walls will form the primary structural system. Braced frames provide lateral stability against wind loads, while shear walls are highly effective in resisting seismic forces. The interaction between these elements is crucial; the shear walls absorb a significant portion of the seismic load, reducing the demands on the braced frames. Imagine a skeleton with strong bones (shear walls) and supporting ligaments (braced frames).
This system ensures the building can withstand both wind and earthquake events effectively. Detailed finite element analysis would be required to accurately model the stress distribution within the structure.
Exterior Walls
Exterior walls contribute to the building’s aesthetic appeal, but also serve vital structural and environmental roles. They are designed for thermal performance, waterproofing, and wind resistance. High-performance curtain walls, consisting of glass panels and aluminum framing, are commonly used in high-rise buildings. These walls are lightweight, allowing for reduced structural demands while still offering good thermal insulation and wind resistance.
The design will incorporate advanced sealants and glazing systems to ensure waterproofing and energy efficiency.
Interior Columns and Beams
Interior columns and beams transfer gravity loads from the floors and roof to the foundation. High-strength steel sections will be used for columns, ensuring sufficient capacity to carry the axial loads and moments resulting from gravity loads. Beams, also made of steel, will support the floor systems and transfer loads to the columns. The arrangement of columns and beams will be optimized to minimize deflections and maximize load distribution efficiency.
Floor Systems
Composite steel deck systems are often preferred for high-rise buildings due to their high strength-to-weight ratio and efficient load transfer. The steel deck acts compositely with a concrete slab, forming a strong and stiff floor system. The design considers live load requirements, deflection limits, and fire resistance. Detailed calculations would involve analyzing the flexural capacity of the composite section and ensuring it meets the design requirements.
Material Properties
| Material | Yield Strength (MPa) | Tensile Strength (MPa) | Compressive Strength (MPa) | Elastic Modulus (GPa) ||—————–|———————-|———————–|————————–|———————–|| High-Strength Steel | 500 | 600 | – | 200 || High-Performance Concrete |
- |
- | 80 | 30 |
Column Design Calculation (Simplified Example)
Let’s consider a typical interior column subjected to combined axial load (P = 2000 kN) and bending moment (M = 500 kNm). Using a simplified interaction equation for steel columns (ignoring second-order effects for this illustration):
P/Py + 8M/P y*r ≤ 1
Where P y is the yield load and r is the radius of gyration of the column section. A suitable column section would be selected based on this equation and other design constraints. This is a simplified example; actual column design requires more rigorous analysis using advanced structural analysis software.
Challenges and Innovations
Designing high-rise buildings presents significant challenges. Wind sway is mitigated through the use of tuned mass dampers, which counter the building’s movement. Seismic resilience is improved through base isolation systems, which decouple the building from the ground motion. Material limitations are addressed through the development of high-performance materials with enhanced strength and durability. The future of high-rise design lies in the integration of smart technologies and sustainable practices, leading to more resilient, efficient, and environmentally friendly structures.
Answers to Common Questions
What are some common pitfalls in theoretical construction?
Common pitfalls in theoretical construction include confirmation bias (favoring evidence that supports pre-existing beliefs), flawed research design, insufficient data, and a failure to adequately address alternative explanations.
How does social construction impact the built environment?
Social construction significantly influences the built environment by shaping design preferences, defining the function and purpose of spaces, and dictating accessibility and inclusivity. Cultural norms and societal values are directly reflected in architectural styles, urban planning, and the overall use of space.
What is the role of ethics in both theoretical and physical construction?
Ethical considerations are paramount in both theoretical and physical construction. In theory, ethical conduct ensures the responsible use of research, avoiding bias and ensuring transparency. In physical construction, ethical practices encompass worker safety, environmental responsibility, and adherence to building codes and regulations.
How can advancements in AI impact future construction practices?
AI promises to revolutionize construction through improved design optimization, predictive maintenance, enhanced safety protocols, and automated construction processes. However, ethical concerns around job displacement and algorithmic bias must be carefully addressed.