Do amp voltage resistance machines use electron theory? Absolutely. The operation of all DC machines fundamentally relies on the movement of electrons within conductors subjected to magnetic fields. Ignoring electron theory renders the entire system inexplicable. This exploration delves into the intricate dance between electrons, magnetic fields, and the resulting voltage and current within these machines, revealing the precise mechanisms driving their power and functionality.
Understanding how electron flow dictates the behavior of DC motors and generators is paramount. From the generation of back EMF to the precise control of speed and torque, the underlying principles of electron behavior are indispensable. This analysis will examine these principles in detail, providing a clear and concise explanation of the electron’s pivotal role in the functioning of these essential machines.
Introduction to DC Machines
The world of electricity hums with the tireless work of direct current (DC) machines, unsung heroes powering countless applications from tiny toys to massive industrial equipment. Their elegance lies in their simplicity and robustness, a testament to fundamental electromagnetic principles that continue to shape our technological landscape. Understanding their operation unlocks a deeper appreciation for the ingenuity of electrical engineering.
Fundamental Principles of DC Machines
At the heart of every DC machine lies Faraday’s Law of Electromagnetic Induction: a changing magnetic field induces a voltage in a conductor. This is the bedrock of both DC generators and motors. Imagine a conductor moving through a magnetic field; the magnetic flux lines are cut, inducing a voltage. The magnitude of this induced voltage (E) is directly proportional to the rate of change of magnetic flux (Φ) linked with the conductor, mathematically represented as:
E = -N(dΦ/dt)
where N is the number of turns in the coil. The negative sign indicates the direction of the induced voltage, as defined by Lenz’s Law. This induced voltage is the source of power in a generator. Conversely, in a motor, applying a voltage across a conductor in a magnetic field results in a force (F) acting on the conductor, given by:
F = BILsinθ
where B is the magnetic flux density, I is the current flowing through the conductor, L is the length of the conductor within the magnetic field, and θ is the angle between the conductor and the magnetic field. This force is the driving mechanism behind motor rotation. A crucial aspect of motor operation is back EMF (electromotive force), a voltage generated by the rotating armature that opposes the applied voltage.
Yes, amp voltage resistance machines fundamentally rely on electron theory; their operation hinges on the flow and behavior of electrons. For a deeper understanding of the underlying physics, consult the comprehensive resources available at the blueconic knowledge base , which offers detailed explanations of electrical principles. This knowledge is crucial for comprehending how these machines manipulate voltage and current through electron movement.
This back EMF is directly proportional to the speed of the motor. It plays a vital role in regulating motor current and protecting it from excessive current draw. A simple diagram would show a conductor moving perpendicularly through magnetic flux lines, with arrows indicating the direction of the magnetic field, conductor movement, and induced current.
Components of DC Motor and Generator, Do amp voltage resistance machines use electron theory
DC machines, whether motors or generators, share a common set of core components. The armature, the rotating part, houses the conductors that carry the current. Its construction involves a cylindrical core (often laminated to minimize eddy current losses) with slots to accommodate the windings. Lap and wave windings are two common types, differing in the way they connect the conductors to the commutator, impacting the voltage and current characteristics.
A cross-sectional diagram would reveal the layered structure of the armature, with windings neatly placed in the slots. The field poles, typically electromagnets, create the magnetic field necessary for induction. These can be salient (projecting poles) or non-salient (smooth cylindrical structure), each with its own design advantages. The yoke, the outer frame, provides mechanical support and completes the magnetic circuit, typically made of ferromagnetic materials with high permeability and low reluctance.
Brushes, typically made of carbon, rest on the commutator, a segmented cylindrical structure integral to the armature. The commutator’s role is pivotal: in generators, it converts the alternating current induced in the armature windings into a direct current output. In motors, it ensures unidirectional torque by reversing the current in the armature windings at the appropriate instants.
A diagram illustrating the brush-commutator interaction would show the brushes making contact with the commutator segments, demonstrating the current reversal. Other essential components include bearings, which support the rotating armature, and end bells, which enclose the machine and provide protection.
Comparison of DC Machine Windings
The method of connecting the field windings to the armature significantly impacts the performance characteristics of a DC machine. Series, shunt, and compound windings represent three distinct configurations.A schematic diagram for each winding type would clearly show the connection between the field and armature windings.Series wound DC machines exhibit high starting torque but poor speed regulation. Their torque-speed curve would show a steep downward slope.
They are ideal for applications requiring high starting torque, such as cranes and electric vehicles.Shunt wound DC machines offer relatively constant speed under varying loads. Their torque-speed curve would show a gentler slope. They are well-suited for applications requiring constant speed, such as pumps and fans.Compound wound DC machines combine the characteristics of series and shunt windings. They provide a balance between high starting torque and good speed regulation.
Their torque-speed curve would fall between that of series and shunt machines. They find use in applications needing a compromise between high starting torque and stable speed, such as elevators and rolling mills.A table summarizing the key differences would compare torque-speed characteristics, starting torque, speed regulation, efficiency, and applications for each winding type. For instance, series-wound motors would be characterized by high starting torque and poor speed regulation, suitable for applications like electric cranes.
Shunt-wound motors would show relatively constant speed and moderate starting torque, ideal for applications like fans. Compound-wound motors would represent a balance, making them suitable for elevators and rolling mills.
Electron Flow in DC Machines
The heart of every DC machine beats with the rhythmic pulse of electrons, a microscopic current orchestrating the macroscopic power we harness. Understanding this electron flow is key to grasping the fundamental principles governing these workhorses of electrical engineering. This section delves into the intricate dance of electrons within the magnetic fields of DC machines, revealing the secrets behind their operation.
Detailed Description of Electron Movement
The movement of electrons within a DC machine’s conductors is a fascinating interplay of electric and magnetic forces. When a conductor carrying a current is placed within a magnetic field, the electrons within that conductor experience a force, as described by Fleming’s left-hand rule. Imagine a conductor, its electrons drifting along its length. Now, place this conductor within a magnetic field.
The magnetic field exerts a force on these moving electrons, perpendicular to both the direction of electron flow and the magnetic field lines. This force is what creates the rotational motion in a DC motor.A simple diagram can illustrate this: Draw a conductor represented by a straight line. Arrows indicate the direction of electron flow (conventionally opposite to current flow).
Then, draw magnetic field lines intersecting the conductor at right angles. Finally, add a curved arrow representing the direction of the force on the electrons, as determined by Fleming’s left-hand rule. This force is responsible for the torque generated in a DC motor.Let’s visualize electron flow in a separately excited DC motor. Imagine a cross-sectional view. The armature, a cylindrical structure, houses numerous coils of wire.
These coils are connected to the commutator, a segmented cylindrical structure. Carbon brushes make contact with the commutator, providing the path for current to flow into and out of the armature. As the armature rotates, the commutator segments switch the current direction in the armature coils, ensuring continuous unidirectional torque. In the diagram, trace the path of electron flow from the negative terminal of the power supply, through the brushes, into the armature windings, and back to the positive terminal.
Show how the commutator changes the current direction in the coils as the armature rotates, maintaining a constant direction of torque.A small DC motor, say a 12V, 10W motor, might have an armature current on the order of 1 Ampere. This current represents the collective flow of billions upon billions of electrons surging through the armature windings.
Magnetic Field’s Role in Directing Electron Flow
The magnetic field strength is directly proportional to the force acting on the electrons. A stronger magnetic field leads to a greater force, and consequently, more torque in a motor. This relationship is expressed mathematically by the Lorentz force equation:
F = qvBsinθ
where F is the force, q is the electron charge, v is the electron velocity, B is the magnetic field strength, and θ is the angle between the velocity and the magnetic field.Magnetic fields in DC machines can be generated using permanent magnets or electromagnets. Permanent magnets offer simplicity and require no external power, but their field strength is fixed.
Electromagnets, on the other hand, provide greater control over the magnetic field strength, allowing for variable speed and torque control. However, they require additional power for their operation, impacting overall efficiency. Permanent magnet motors are generally more efficient at lower power levels due to reduced losses, while electromagnets provide flexibility for higher power applications and more precise control.Armature reaction, the magnetic field generated by the armature current, can distort the main magnetic field.
This distortion can lead to non-uniform force on the electrons, resulting in reduced efficiency and potential commutation problems.
Commutator’s Role in Unidirectional Current
The commutator is the ingenious heart of the DC machine, ensuring that the torque produced by the interaction of the magnetic field and electron flow remains unidirectional despite the rotating armature. It consists of a series of insulated copper segments, each connected to an armature coil. As the armature rotates, the commutator segments make and break contact with the brushes, reversing the current direction in the armature coils at precisely the right moment.
A series of diagrams showing the commutator segments and brush positions at different stages of rotation would clearly demonstrate this switching action and its effect on the current direction in the external circuit. Show how the current flows through different armature coils as the rotor turns.Commutation is the process of transferring current from one set of armature coils to another as the commutator segments switch under the brushes.
Precise timing is critical to avoid sparking, which can damage the commutator and brushes.Sparking can occur due to several factors, including brush wear, high current, or poor commutation timing. Solutions include using high-quality brushes, ensuring proper brush pressure, and optimizing the design of the commutator and armature windings.
Comparative Analysis
Feature | Permanent Magnet DC Machine | Electromagnet DC Machine |
---|---|---|
Magnetic Field | Fixed strength, provided by permanent magnets; inherently stable. | Variable strength, controlled by field current; stability depends on control system. |
Efficiency | Generally higher efficiency at lower power levels due to absence of field winding losses. Typically 70-90%. | Efficiency can be lower at lower power levels due to field winding losses. Efficiency typically 60-85%, but can be higher with advanced designs. |
Cost | Generally lower initial cost due to simpler construction. | Higher initial cost due to the added complexity of the electromagnet system. |
Controllability | Limited speed and torque control; speed primarily controlled by voltage. | Excellent speed and torque control through adjustment of field and armature currents. |
Maintenance | Lower maintenance requirements; mainly brush replacement. | Higher maintenance requirements; includes brush replacement and potential issues with field windings. |
Voltage Generation in DC Machines
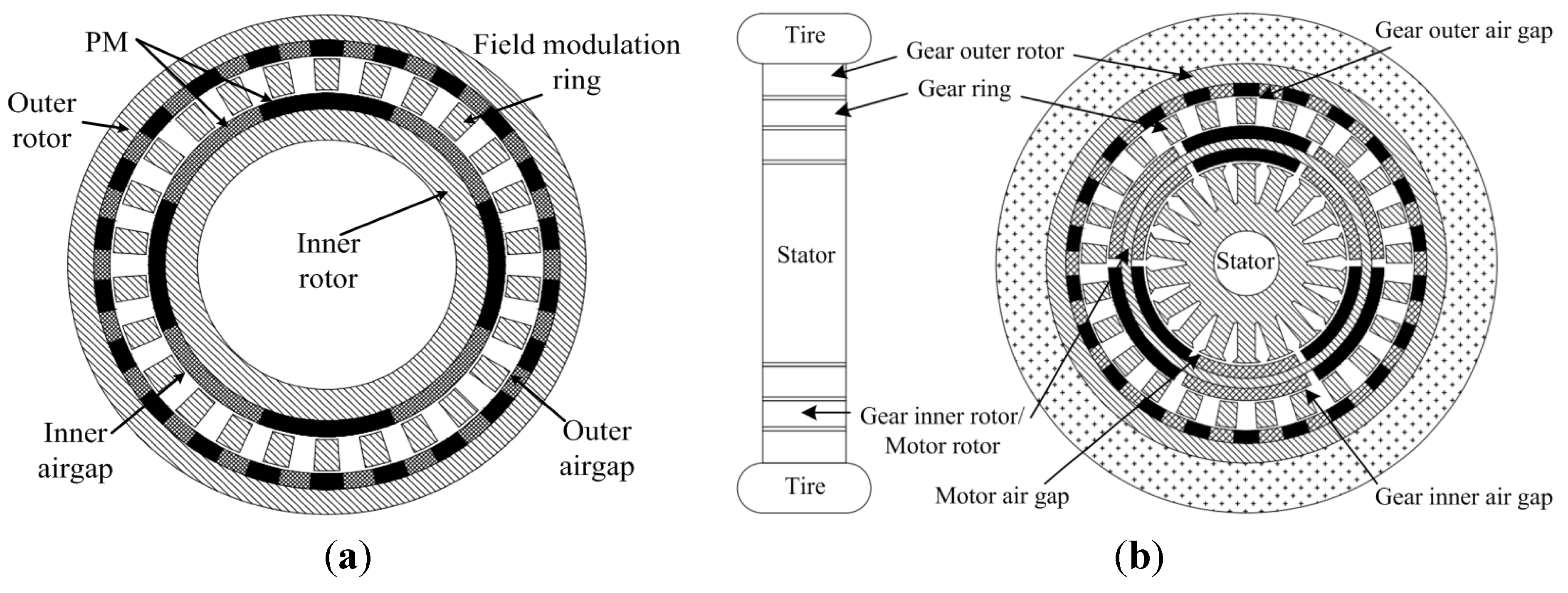
The heart of a DC generator lies in its ability to convert mechanical energy into electrical energy, a process deeply rooted in the principles of electromagnetic induction. This transformation, seemingly magical, is elegantly explained by Faraday’s Law and the ingenious design of the DC machine itself. Understanding this process unlocks the secrets behind the smooth, direct current that powers countless applications.
Electromagnetic Induction in DC Generators
Faraday’s Law of Induction is the cornerstone of DC generator operation. It states that a changing magnetic field induces a voltage in a conductor. In a DC generator, this changing magnetic field is created by rotating a conductor within a stationary magnetic field. As the conductor cuts through the magnetic flux lines, a voltage is induced across its ends.
However, this induced voltage is alternating current (AC), constantly changing direction. The commutator, a cleverly designed segmented ring, plays a crucial role here. By switching the connections to the external circuit at precisely the right moment, the commutator rectifies the AC voltage, delivering a pulsating but unidirectional DC voltage to the load. This ingenious mechanism transforms the inherently alternating nature of the induced EMF into the direct current characteristic of DC generators.The magnitude of the induced voltage (EMF) depends on several factors.
Firstly, a stronger magnetic field leads to a larger induced voltage. Secondly, more conductors cutting the magnetic field result in a higher voltage. Finally, a faster rotation speed increases the rate at which the conductors cut the magnetic flux lines, directly impacting the induced voltage. These relationships can be mathematically represented as:
E = KΦZNp/60A
where:* E is the generated EMF (volts)
- K is a constant that depends on the generator’s construction
- Φ is the magnetic flux per pole (webers)
- Z is the total number of conductors
- N is the rotational speed (revolutions per minute)
- p is the number of poles
- A is the number of parallel paths in the armature
The generated EMF, however, is not the same as the terminal voltage. Internal resistance within the armature causes a voltage drop (I aR a), where I a is the armature current and R a is the armature resistance. Armature reaction, the magnetic field distortion caused by the armature current, further reduces the terminal voltage. Therefore, the terminal voltage (V t) is given by:
Vt = E – I aR a
Armature reaction voltage drop
Relationship between Magnetic Flux, Conductor Velocity, and Induced Voltage
The induced voltage in a conductor moving within a magnetic field is directly proportional to the magnetic flux density (B), the length of the conductor (l) within the field, and the velocity (v) of the conductor perpendicular to the field. This relationship can be expressed using vector notation as:
E = (v x B) • l
where:* E is the induced electromotive force (a vector)
- v is the velocity vector of the conductor
- B is the magnetic flux density vector
- l is the vector representing the length of the conductor
The dot product indicates that only the component of the conductor’s velocity perpendicular to the magnetic field contributes to the induced voltage. When the conductor moves parallel to the magnetic field, the induced voltage is zero. A graphical representation would show a sinusoidal waveform, peaking when the conductor’s motion is perpendicular to the magnetic field and reaching zero when parallel.
The x-axis would represent the angle between the conductor’s velocity and the magnetic field, while the y-axis would represent the induced voltage.For example, consider a conductor of length 1 meter moving at a velocity of 10 m/s perpendicular to a magnetic field of 1 Tesla. The induced voltage would be:
E = Blv = (1 T)(1 m)(10 m/s) = 10 V
This calculation assumes a uniform magnetic field and a conductor moving at a constant velocity perpendicular to the field.
Diagram and Voltage Representation in a DC Generator
Imagine a simplified two-pole DC generator. A rectangular armature rotates within the magnetic field created by two field poles (North and South). The armature windings are connected to commutator segments, which in turn are contacted by brushes to provide a continuous flow of current to the external circuit.
Time (ms) | Commutator Segment Position | Voltage at Positive Brush (V) | Voltage at Negative Brush (V) |
---|---|---|---|
0 | Segment 1 | +5 | -5 |
10 | Segment 2 | +5 | -5 |
20 | Segment 3 | +5 | -5 |
30 | Segment 4 | +5 | -5 |
40 | Segment 1 | +5 | -5 |
This table shows a simplified representation; the actual voltage waveform is pulsating but remains unidirectional.
Time (ms) | Generated Voltage (Before Commutation) | Generated Voltage (After Commutation) |
---|---|---|
0 | +5 | +5 |
10 | -5 | +5 |
20 | +5 | +5 |
30 | -5 | +5 |
The key difference is the rectification of the AC waveform into a pulsating DC waveform by the commutator.
Advanced Considerations
Armature reaction, the magnetic field distortion caused by the armature current, weakens the main field and reduces the generated voltage. Compensating windings, placed within the armature slots, counteract this effect by generating a magnetic field that opposes the armature reaction field.Different types of DC generators exist, each with unique characteristics:
Generator Type | Field Winding Connection | Voltage Characteristics | Applications |
---|---|---|---|
Separately Excited | Independent excitation | Constant voltage | Precise voltage control applications |
Shunt | Parallel to armature | Slightly drooping voltage | General-purpose applications |
Series | Series with armature | Highly variable voltage | Constant-current applications |
Compound | Both shunt and series | Flat-compounded or over-compounded | Wide range of applications |
Generated voltage can be controlled by adjusting the field current (which affects the magnetic flux) or by changing the speed of rotation. A block diagram of a typical voltage control system would show a feedback loop that compares the desired voltage with the actual voltage and adjusts the field current accordingly.
Voltage and Current Relationships
The heart of any DC machine beats to the rhythm of voltage and current, a dance governed by fundamental electrical principles. Understanding their intricate relationship is crucial to mastering the operation and application of these powerful devices. This section delves into the precise interplay of voltage and current in various DC machine configurations, revealing the elegance and power hidden within their seemingly simple designs.
We will explore how Ohm’s Law provides a foundational understanding of this relationship and how it manifests differently across different DC machine types.
Ohm’s Law, that cornerstone of electrical engineering, elegantly describes the relationship between voltage (V), current (I), and resistance (R) in a DC circuit:
V = IR
. This simple equation forms the bedrock of our understanding of DC machine behavior. In a DC motor, for example, the applied voltage drives the current through the armature windings, overcoming the internal resistance and generating the necessary torque. Conversely, in a DC generator, the mechanical rotation induces a voltage, which then dictates the current flowing through the load connected to the generator’s terminals.
The resistance of the windings, brushes, and the external load all play a crucial role in determining the final current.
Ohm’s Law Application in DC Machine Circuits
Applying Ohm’s Law to DC machines requires careful consideration of the different components and their respective resistances. The armature circuit, for instance, includes the armature winding resistance (Ra), and the field circuit involves the field winding resistance (Rf). Consider a shunt-wound DC motor: the field winding is connected in parallel with the armature. The voltage across both is the same (the supply voltage Vs), but the currents are different, governed by their respective resistances.
The armature current (Ia) is calculated as Ia = (Vs – Eb)/Ra, where Eb is the back EMF generated by the motor. This back EMF acts as a counter-voltage, opposing the supply voltage and regulating the armature current. The field current (If) is simply If = Vs/Rf. The total current drawn from the supply is the sum of the armature and field currents: It = Ia + If.
This detailed analysis showcases how Ohm’s Law is not just a simple formula, but a powerful tool for understanding the complex interplay of voltage and current within a DC machine.
Voltage and Current Characteristics of Different DC Machine Types
Different types of DC machines exhibit unique voltage and current characteristics due to their distinct field winding configurations. Series-wound motors, for example, have their field winding connected in series with the armature. This arrangement leads to a high starting torque but a significant increase in current with increasing speed. In contrast, shunt-wound motors, with their field winding connected in parallel with the armature, exhibit relatively constant speed characteristics over a wider range of loads.
Compound-wound motors, combining series and shunt field windings, offer a balance between the characteristics of the series and shunt types, providing both high starting torque and relatively stable speed regulation. Understanding these differences is vital for selecting the appropriate DC machine for a given application, ensuring optimal performance and efficiency.
Key Equations Governing Voltage and Current Relationships in DC Machines
A concise summary of the key equations governing voltage and current relationships in DC machines provides a powerful reference for further analysis and design. These equations encapsulate the essence of DC machine behavior, allowing for precise prediction and control.
- Ohm’s Law:
V = IR
where V is voltage, I is current, and R is resistance.
- Armature Current (DC Motor):
Ia = (Vs – Eb)/Ra
where Ia is armature current, Vs is supply voltage, Eb is back EMF, and Ra is armature resistance.
- Field Current (DC Motor):
If = Vs/Rf
where If is field current, Vs is supply voltage, and Rf is field resistance.
- Total Current (DC Motor):
It = Ia + If
where It is total current drawn from the supply.
- Generated Voltage (DC Generator):
Eg = KφN
where Eg is generated voltage, K is a constant, φ is the magnetic flux, and N is the speed of rotation.
Resistance in DC Machines
The seemingly simple act of generating electricity in a DC machine is, in reality, a complex dance of electrons, magnetic fields, and, crucially, resistance. Understanding resistance is key to appreciating the efficiency and performance limitations of these vital machines. Without this understanding, we remain blind to the subtle forces that govern their power output and longevity.Resistance in a DC machine isn’t a single, monolithic entity; rather, it’s a multifaceted phenomenon distributed across several key components.
Each component contributes its own share of resistance, collectively impacting the machine’s overall efficiency and operational characteristics. The fight against these resistive forces is a constant battle in the quest for optimal performance.
Sources of Resistance in DC Machines
Resistance within a DC machine arises from several sources, each with its own unique properties and impact on the machine’s operation. These sources, primarily the armature windings, the field windings, and the brushes, act as obstacles to the smooth flow of electrons, leading to energy losses in the form of heat. This heat generation is a significant concern, not only affecting efficiency but also potentially damaging the machine if allowed to escalate unchecked.
Impact of Resistance on Machine Efficiency and Performance
The presence of resistance in a DC machine inevitably leads to power losses. These losses manifest primarily as heat dissipation within the machine’s components. Higher resistance means more energy is converted into heat rather than useful mechanical work, directly reducing the machine’s efficiency. This decrease in efficiency translates to higher operating costs, reduced lifespan, and a diminished capacity to perform its intended function.
For example, in a large industrial motor, even a small increase in resistance could translate to significant losses in power and a substantial increase in cooling requirements. This impact reverberates throughout the entire system, affecting not just the machine itself but also the overall energy consumption and operational expenses. The consequences of neglecting resistance are far-reaching and impactful.
Typical Resistance Values in DC Machines
The following table provides typical resistance values for various components in a DC machine. These values are approximate and can vary significantly depending on the machine’s size, design, and operating conditions. Remember that these are representative values; actual resistances will vary depending on the specific machine and its manufacturing specifications.
Component | Resistance (Ω) | Typical Range (Ω) | Notes |
---|---|---|---|
Armature | 0.1 – 1.0 | 0.05 – 2.0 | Highly dependent on the size and construction of the armature windings. |
Field Windings | 10 – 100 | 5 – 200 | Varies significantly based on the field winding design and the required field strength. |
Brushes | 0.01 – 0.1 | 0.005 – 0.2 | Relatively low resistance, but significant contact resistance can impact performance. |
Total Resistance | 10 – 111 | 5 – 212 | The sum of armature, field, and brush resistances. |
Power and Efficiency in DC Machines
The heart of a DC machine’s operation beats with the rhythm of power conversion – transforming electrical energy into mechanical energy (in motors) or vice versa (in generators). Understanding the power relationships and the factors influencing efficiency is crucial for optimizing their performance and longevity. Efficiency, in this context, represents a poignant dance between the energy put in and the useful work extracted, a measure of how effectively the machine performs its intended task.
Let’s delve into the intricate details of this energetic ballet.The power relationships in DC motors and generators are governed by fundamental electrical and mechanical principles. In a motor, electrical power supplied is converted into mechanical power output, while in a generator, mechanical power input is transformed into electrical power output. This conversion, however, isn’t perfect; some energy is inevitably lost as heat.
This loss significantly impacts the overall efficiency of the machine. The efficiency is expressed as the ratio of output power to input power, often represented as a percentage. A higher efficiency signifies less energy wasted as heat, resulting in better performance and cost savings.
Power Relationships in DC Machines
In a DC motor, the input electrical power (Pin) is given by the product of the armature voltage (Va) and the armature current (Ia):
Pin = V aI a
. The output mechanical power (Pout) is calculated by the product of the torque (T) and the angular speed (ω):
Pout = Tω
. The efficiency (η) is then:
η = (Pout / P in)100%
. In a DC generator, the input mechanical power is the driving force, and the output electrical power is the generated voltage multiplied by the load current. The same efficiency formula applies, highlighting the fundamental equivalence of the power conversion process in both motors and generators. Consider a motor with an input power of 10 kW and an output power of 9 kW.
Its efficiency would be 90%, indicating that 1 kW is lost as heat.
Factors Affecting Efficiency
Several factors influence the efficiency of a DC machine. These include the design and construction of the machine, the quality of materials used, the operating conditions, and the load. For example, higher-quality materials with lower resistance can reduce copper losses, improving efficiency. Similarly, optimal operating conditions, such as appropriate speed and load, minimize losses and maximize efficiency.
The design itself plays a pivotal role, with advanced designs incorporating features to minimize energy loss. A poorly designed machine will inherently exhibit lower efficiency compared to its well-engineered counterpart.
Power Losses in DC Machines
Power losses in a DC machine are broadly categorized into three main types: copper losses, iron losses, and mechanical losses. Understanding these losses is crucial for designing and operating efficient machines.
Copper Losses
Copper losses, also known as I²R losses, arise due to the resistance of the windings in the armature and field circuits. These losses are directly proportional to the square of the current flowing through the windings. They are a significant source of energy loss, especially at higher currents. Minimizing these losses involves using conductors with low resistance, optimizing the design of the windings, and ensuring proper cooling.
Imagine a scenario where a faulty connection increases resistance, dramatically increasing copper losses and reducing efficiency.
Iron Losses
Iron losses are associated with the magnetic core of the machine and consist of hysteresis losses and eddy current losses. Hysteresis losses occur due to the repeated magnetization and demagnetization of the core material, while eddy current losses are caused by circulating currents induced in the core by the changing magnetic field. These losses are dependent on the magnetic flux density and frequency.
Minimizing iron losses involves using high-quality core materials with low hysteresis and high resistivity, employing laminated core construction to reduce eddy currents, and efficient core design. A poorly laminated core, for instance, would suffer significantly higher eddy current losses.
Mechanical Losses
Mechanical losses encompass friction and windage losses. Friction losses arise from the rubbing of the bearings and brushes, while windage losses result from air resistance to the rotating parts of the machine. These losses are dependent on the speed and load of the machine. Minimizing mechanical losses involves using high-quality bearings with low friction, proper lubrication, and aerodynamic design of the rotating parts.
Consider a machine operating at high speed; windage losses would be much higher compared to one operating at a lower speed.
Applications of DC Machines
The versatility of DC machines is truly remarkable, finding applications across a vast spectrum of industries and everyday life. Their ability to provide precise speed control and high starting torque, coupled with the relative simplicity of their design, makes them invaluable in numerous scenarios. Let’s delve into the fascinating world of DC machine applications, exploring both motors and generators and the specific types best suited for different tasks.
Real-World Applications of DC Motors and Generators
DC motors and generators, while seemingly simple, are workhorses in a multitude of applications. The choice of motor or generator type (series, shunt, compound, or permanent magnet) is crucial, as it directly impacts performance and efficiency.
DC Motors:
Understanding how amp, voltage, and resistance machines function fundamentally relies on electron theory, describing the flow of charge. This micro-level perspective contrasts sharply with the abstract world of topos theory, where the question of whether are functors used in topos theory is central to its mathematical framework. Returning to the practical, electron theory’s principles are crucial for predicting and controlling the behavior of these machines.
- Electric Vehicles (Permanent Magnet DC Motor): These motors, often in the 50-200 kW range, provide excellent torque at low speeds, crucial for acceleration and hill climbing. The permanent magnet design simplifies the system, reducing cost and complexity.
- Crane Hoists (Series DC Motor): Series motors are ideal for this high-torque, low-speed application because they deliver exceptional starting torque, essential for lifting heavy loads. Power ratings can vary widely, from tens to hundreds of kilowatts, depending on the crane’s capacity.
- Small Appliances (Permanent Magnet DC Motor): Fans, blenders, and other small appliances commonly utilize low-power (under 1 kW) permanent magnet DC motors for their simplicity, cost-effectiveness, and ease of control.
- Industrial Robots (Shunt or Compound DC Motor): Precise speed control is paramount in robotics. Shunt or compound wound motors, often in the 1-10 kW range, provide the necessary speed regulation and torque characteristics for intricate movements.
- Traction Motors in Electric Trains (Series DC Motor): High starting torque is critical for accelerating heavy trains. Series motors, with power ratings in the megawatt range, are frequently employed for this purpose.
DC Generators:
- Emergency Power Systems (Shunt DC Generator): Shunt generators provide stable voltage output, making them suitable for backup power supplies where consistent voltage is essential. Power ratings vary depending on the size of the system.
- Battery Charging Systems (Shunt DC Generator): These generators are used to charge batteries in various applications, offering a controlled and stable voltage source. Power ratings depend on the battery bank’s size and charging requirements.
- Excitation Systems for AC Generators (Shunt DC Generator): Many AC generators require a DC excitation source, and shunt generators are often used for this purpose due to their stable voltage output. Power ratings are typically in the kilowatt range.
- Small Wind Turbines (Permanent Magnet DC Generator): Permanent magnet generators are simple and cost-effective, making them suitable for small-scale wind power generation. Power output is relatively low, typically in the kilowatt range.
- Arc Welding Machines (Series DC Generator): The high current and variable voltage characteristics of series generators make them well-suited for arc welding applications. Power ratings vary depending on the welding application.
Suitability of Different DC Machine Types for Specific Applications
The choice of DC motor type significantly impacts the performance of a system. Let’s compare series, shunt, and compound motors for three distinct applications.
Low-Speed, High-Torque Application (Crane Hoist): A series motor excels here. Its speed-torque curve shows high torque at low speeds, ideal for lifting heavy loads. Shunt motors have lower starting torque, while compound motors offer a compromise, but the series motor’s superior starting torque is crucial for this application.
High-Speed, Low-Torque Application (Computer Fan): A shunt motor is well-suited for this application. Its speed-torque curve shows relatively constant speed over a range of loads. Series motors would be unsuitable due to their tendency to run at dangerously high speeds under light loads. Compound motors could also work but are generally more complex and expensive.
Application Requiring Precise Speed Control (Robotic Arm): Shunt and compound motors are both viable options, offering good speed regulation through field control. The choice between them often comes down to cost and the precise balance between speed regulation and torque requirements. Series motors are less suitable due to their poor speed regulation.
Applications Categorized by DC Machine Type
Machine Type | Application Description | Power Rating Range | Reason for Choice |
---|---|---|---|
Series | Crane Hoist | 10-500 kW | High starting torque |
Series | Electric Vehicle Traction Motor | 50-200 kW | High torque at low speeds |
Shunt | Battery Charger | 1-10 kW | Stable voltage output |
Shunt | Computer Fan | <1 kW | Constant speed operation |
Shunt | Small Wind Turbine Generator | 1-5 kW | Stable voltage output |
Compound | Industrial Robot | 1-10 kW | Good speed regulation and torque |
Compound | Elevator | 10-100 kW | Balance of speed and torque control |
Permanent Magnet | Electric Vehicle | 50-200 kW | High efficiency, simplicity |
Permanent Magnet | Small Appliances | <1 kW | Cost-effectiveness, ease of control |
Permanent Magnet | Hybrid Vehicle Starter Motor | 5-15 kW | High efficiency and quick response |
Advantages and Disadvantages of Permanent Magnet vs. Wound-Field DC Motors
In applications like electric vehicles, permanent magnet DC motors offer higher efficiency and reduced maintenance due to the absence of field windings. However, they can be more expensive initially and their magnetic field strength is fixed, limiting flexibility in speed control. In contrast, wound-field motors are more versatile, allowing for adjustable field strength and thus better speed control, but they are less efficient and require more maintenance.
In applications such as industrial robots requiring precise speed control and adjustable torque, the benefits of a wound-field motor’s adjustability might outweigh the higher cost and maintenance needs. For low-cost, low-power applications like small fans, permanent magnet motors are often preferred for their simplicity and lower cost.
Speed-Torque Characteristics of Series, Shunt, and Compound DC Motors
The speed-torque curves of these motors differ significantly. A series motor exhibits high torque at low speeds, dropping sharply as speed increases. A shunt motor has a relatively flat speed-torque curve, maintaining relatively constant speed over a range of loads. A compound motor offers a compromise, combining characteristics of both series and shunt motors, resulting in a curve that falls between the two.Simplified ASCII representation (Note: This is a very simplified representation, actual curves are smoother):Series: /\Shunt: —-Compound: -/-\These differences in speed-torque characteristics determine the suitability of each motor type for specific applications.
Impact of Advancements in Power Electronics
Advancements in power electronics, particularly the use of IGBTs and MOSFETs, have revolutionized DC machine control. These switching devices allow for highly efficient and precise control of motor speed and torque, enabling the use of DC machines in applications previously deemed unsuitable. This has led to increased efficiency and greater precision in applications such as robotics, electric vehicles, and industrial automation.
Environmental Considerations
The environmental impact of DC machines is primarily related to energy efficiency and the disposal of components at the end of their lifespan. Highly efficient machines minimize energy consumption, reducing greenhouse gas emissions. Proper recycling of materials such as copper and magnets is crucial to mitigate environmental impact at the end of a machine’s life cycle.
Key Considerations for DC Machine Selection: The selection of a DC machine depends critically on the application’s requirements for speed, torque, and efficiency. Cost and maintenance requirements are also vital factors. For high-torque, low-speed applications, a series motor might be suitable, while high-speed, low-torque applications may benefit from a shunt motor. Applications demanding precise speed control often use shunt or compound motors. Permanent magnet motors offer high efficiency but may be more expensive. A careful assessment of all these factors is essential for optimal performance and cost-effectiveness.
Speed Control of DC Motors
The ability to precisely control the speed of a DC motor is paramount in countless applications, from the delicate movements of robotic arms to the powerful thrust of electric vehicles. The inherent flexibility of DC motors allows for a variety of speed control methods, each with its own strengths and weaknesses. Understanding these methods is crucial for selecting the optimal approach for a given application, ensuring efficiency, longevity, and performance.
Speed control in DC motors is achieved primarily by manipulating either the armature voltage or the field flux. These manipulations alter the motor’s back EMF (electromotive force), which directly influences its rotational speed. The choice of method depends on factors such as the required speed range, precision, cost, and efficiency considerations. Let’s delve into the most common techniques.
Armature Voltage Control
Armature voltage control is a straightforward method that involves varying the voltage applied to the armature winding. This directly affects the armature current and consequently the motor’s torque and speed. Reducing the armature voltage lowers the speed, while increasing it raises the speed. This method is relatively simple to implement, using techniques such as pulse width modulation (PWM) for precise control.
However, it can lead to reduced efficiency at lower speeds due to increased armature current for the same torque.
Field Flux Control
Field flux control manipulates the magnetic field strength generated by the field winding. Weakening the field flux increases the motor speed, while strengthening it reduces the speed. This method offers a wider speed range compared to armature voltage control, but it requires more complex circuitry and can lead to instability at very low field fluxes. Furthermore, weakening the field flux can result in higher speeds with potentially increased risk of damage from centrifugal forces if not carefully managed.
Combined Armature Voltage and Field Flux Control
For optimal performance and a wide speed range, a combination of armature voltage and field flux control is often employed. This synergistic approach allows for precise speed regulation across a broad spectrum. By carefully coordinating adjustments to both the armature voltage and field flux, engineers can optimize efficiency and minimize the drawbacks associated with using either method alone. This method, while more complex to implement, is often the preferred solution for demanding applications requiring precise speed control across a wide range.
Comparison of Speed Control Techniques
The following table summarizes the advantages and disadvantages of the discussed speed control methods:
Method | Advantages | Disadvantages |
---|---|---|
Armature Voltage Control | Simple implementation, good for low-speed applications | Reduced efficiency at lower speeds, limited speed range |
Field Flux Control | Wider speed range, good efficiency at higher speeds | Complex circuitry, potential instability at low fluxes |
Combined Control | Wide speed range, good efficiency, precise control | More complex implementation |
Flowchart for Armature Voltage Control using PWM
The following flowchart illustrates the steps involved in implementing armature voltage control using Pulse Width Modulation (PWM). PWM efficiently controls the average voltage applied to the motor by varying the duty cycle of a switching signal.
Imagine a simple system where a microcontroller acts as the brain of the operation. It receives a desired speed signal, processes it, and generates a PWM signal. This PWM signal then controls a power transistor (like a MOSFET or IGBT), which switches the voltage on and off rapidly. The faster the switching, the more precisely the average voltage is controlled, and hence the speed of the motor.
(Note: A visual flowchart would be beneficial here, but as per instructions, a textual description is provided instead. The flowchart would visually represent the steps below.)
- Receive desired speed setpoint from user input or control system.
- Convert the speed setpoint into a corresponding duty cycle for the PWM signal.
- Generate the PWM signal using a microcontroller timer.
- Amplify the PWM signal to control the power transistor (MOSFET/IGBT).
- Apply the controlled voltage to the DC motor armature.
- Monitor the motor speed using a feedback sensor (e.g., encoder or tachometer).
- Compare the measured speed with the desired speed and adjust the duty cycle accordingly to maintain the setpoint via a feedback control loop.
Troubleshooting DC Machines
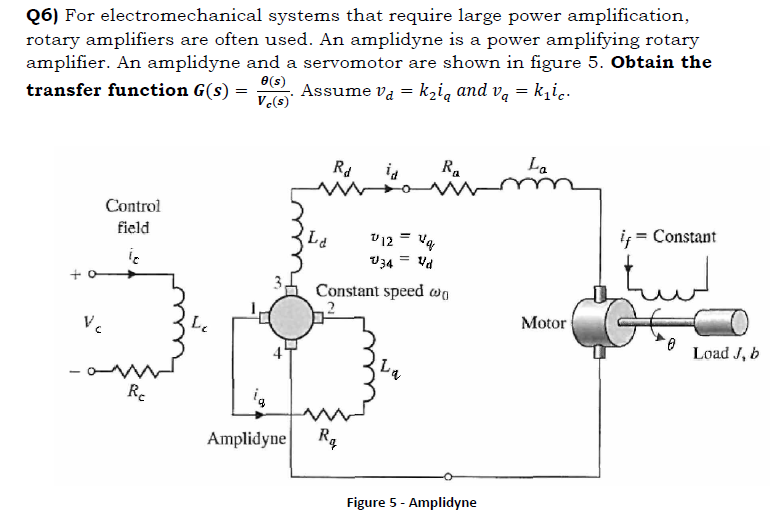
The heart of any DC machine, whether motor or generator, beats with the rhythm of electron flow. When this rhythm falters, diagnosing the problem can feel like deciphering a complex musical score. Understanding the common ailments and employing systematic troubleshooting techniques is crucial for restoring the machine’s functionality and preventing further damage. This section delves into the practical aspects of identifying and resolving issues within these vital electromechanical devices.
Common Faults and Malfunctions
DC machines, despite their robust design, are susceptible to a range of malfunctions. These can stem from issues within the electrical components, the mechanical parts, or a combination of both. A methodical approach, guided by understanding the machine’s operational principles, is essential for effective troubleshooting. Ignoring early warning signs can lead to catastrophic failure and costly repairs.
Troubleshooting Procedures
A systematic approach to troubleshooting DC machines is paramount. This typically involves a series of steps, beginning with visual inspection and progressing to more involved tests. The process often involves using a combination of diagnostic tools, such as multimeters, insulation testers, and specialized DC motor analyzers. Safety precautions are absolutely crucial throughout the entire process, as working with high voltages and rotating machinery presents significant risks.
Diagnostic Tests for DC Machines
Effective diagnosis hinges on the ability to accurately measure key parameters. This involves using appropriate instruments to measure voltage, current, resistance, and insulation resistance across various components of the machine. For example, a low insulation resistance reading between the armature windings and the frame might indicate a ground fault, a common and potentially dangerous problem. Similarly, measuring the armature current can help identify issues with excessive loading or internal short circuits.
Analyzing the voltage across the brushes can reveal problems with the commutator or brush assembly. A thorough examination using these methods, combined with an understanding of the machine’s schematic, is key to accurate diagnosis.
Example: Diagnosing a No-Start Condition in a DC Motor
Consider a scenario where a DC motor fails to start. The troubleshooting process would begin with a visual inspection for obvious problems such as loose connections, damaged wiring, or mechanical obstructions. Next, a multimeter would be used to check the supply voltage, ensuring it’s within the motor’s rated specifications. The motor’s windings would be checked for continuity and insulation resistance to rule out open circuits or shorts.
If these checks yield no immediate results, a more detailed investigation might be required, possibly involving specialized equipment to test the commutator and brushes for wear or damage. The methodical approach, combined with careful measurements, helps isolate the problem efficiently.
Example: Identifying a Generator’s Reduced Output
A DC generator exhibiting reduced output could be due to several factors. Initial checks would focus on the field excitation, ensuring it’s at the correct level. Measurements of the armature current and voltage would be taken to determine if there is excessive internal resistance or a problem with the commutator. Furthermore, the brushes should be examined for wear and proper contact.
If these initial checks don’t identify the root cause, more advanced tests might be needed, potentially involving load testing to determine the generator’s performance under various operating conditions. The systematic approach ensures that each potential cause is addressed before moving to the next.
The Role of the Magnetic Field: Do Amp Voltage Resistance Machines Use Electron Theory
The magnetic field is the heart of a DC machine, the invisible force that orchestrates the dance of electrons and generates the power we harness. Without it, the machine would be nothing more than a collection of inert components. Understanding its creation, control, and interaction with the armature is crucial to comprehending the entire operation of the DC motor or generator.
This section delves into the fascinating interplay between magnetism and electricity within these vital machines.
Creation and Control of the Magnetic Field in a DC Machine
The magnetic field in a DC machine can be generated using permanent magnets or electromagnets. Permanent magnets, such as those found in smaller DC motors, provide a constant magnetic field, simple in design and requiring no external power source. However, their field strength is fixed and cannot be adjusted. Larger DC machines, requiring adjustable field strength for speed and torque control, typically employ electromagnets.
These consist of coils of wire wound around a ferromagnetic core. Passing an electric current through these coils creates a magnetic field whose strength is directly proportional to the current.Field windings are the coils used to create the magnetic field in electromagnets. Their connection to the power supply determines the type of DC machine: Series windings connect the field coils in series with the armature; shunt windings connect them in parallel; and compound windings use a combination of both series and shunt windings.A series winding configuration (illustrated below) results in a strong magnetic field at high currents (and hence high torque at low speeds), but the field strength is directly proportional to the load current, leading to poor speed regulation.[Diagram: A simple schematic of a DC motor with series field winding.
The field coil is shown in series with the armature, connected to a common power source. Arrows indicate current flow.]A shunt winding configuration (illustrated below) provides a relatively constant field strength regardless of the load current, resulting in good speed regulation. However, the starting torque is relatively low.[Diagram: A simple schematic of a DC motor with shunt field winding.
The field coil is shown connected in parallel to the armature, both connected to a common power source. Arrows indicate current flow.]A compound winding configuration (illustrated below) offers a compromise between the two, providing both good starting torque and relatively good speed regulation. It combines both series and shunt windings, often with adjustable shunt field resistance.[Diagram: A simple schematic of a DC motor with compound field winding.
Both series and shunt field coils are shown, connected to a common power source. Arrows indicate current flow.]Field strength is controlled by adjusting the current flowing through the field windings. This is often achieved using a field rheostat, a variable resistor connected in series with the field winding. Field strength is measured in Teslas (T), representing the magnetic flux density.Magnetic saturation occurs when increasing the field current no longer significantly increases the flux density.
This is because the magnetic domains in the core material become fully aligned. A graph showing the relationship between field current and flux density would exhibit a steep initial rise, followed by a gradual flattening as saturation is approached.[Graph: A graph showing the relationship between field current (x-axis) and flux density (y-axis). The curve should show an initial steep rise, followed by a gradual flattening as it approaches saturation.]
Interaction Between the Magnetic Field and the Armature Conductors
Faraday’s Law of Electromagnetic Induction states that a voltage is induced in a conductor when it moves through a magnetic field. In a DC machine, the armature conductors rotate within the magnetic field, inducing a voltage (electromotive force, or EMF). The magnitude of the induced EMF (E) is given by:
E = Blv
where:* B is the magnetic flux density (Teslas)
- l is the length of the conductor in the magnetic field (meters)
- v is the velocity of the conductor (meters/second)
Fleming’s Right-Hand Rule determines the direction of the induced EMF. Point your thumb in the direction of motion, your index finger in the direction of the magnetic field, and your middle finger will point in the direction of the induced current.[Diagram: A visual representation of Fleming’s Right-Hand Rule. The thumb, index finger, and middle finger should be mutually perpendicular.]Magnetic flux linkage refers to the number of magnetic field lines that pass through a coil or conductor.
A higher flux linkage results in a greater induced voltage.The commutator is a crucial component that reverses the current direction in the armature conductors at the appropriate moment. This ensures that the torque produced is unidirectional, allowing for continuous rotation. As the armature rotates, the commutator segments switch the current direction in the conductors, maintaining the same direction of torque.[Diagram: A step-by-step illustration showing how the commutator reverses the current direction in the armature conductors to produce unidirectional torque.
The diagram should show the commutator segments and brushes, with current flow indicated at different stages of rotation.]
Impact of Adjusting the Magnetic Field on Machine Performance
Changing the magnetic field strength directly affects the generated voltage (back EMF) in the armature. Increasing the field strength increases the back EMF, according to the equation E = KΦω, where K is a constant, Φ is the magnetic flux, and ω is the angular speed.
E = KΦω
The magnetic field strength is also directly proportional to the torque produced by the motor. A stronger magnetic field results in a greater torque.[Table: A table comparing torque characteristics at different field strengths. The table should include columns for field strength (Teslas), torque (Newton-meters), and speed (RPM).]Varying the magnetic field strength affects the speed and efficiency of the DC machine.
A graph showing the relationship between field strength and speed would demonstrate a generally inverse relationship (for a constant load), while efficiency might peak at an optimal field strength before decreasing due to saturation or other losses.[Graph: A graph illustrating the relationship between field strength (x-axis) and speed (y-axis) for a constant load. A second graph illustrating the relationship between field strength (x-axis) and efficiency (y-axis) could also be included.]Excessive field strength can lead to magnetic saturation, reducing the effectiveness of further increases in field current.
Insufficient field strength can result in weak torque and reduced efficiency. Solutions include adjusting the field rheostat to achieve the optimal field strength or replacing the field windings if they are damaged or worn.
Advanced Concepts in DC Machine Operation
Delving deeper into the fascinating world of DC machines reveals a captivating interplay of electromagnetic forces and intricate design elements that govern their performance. Understanding these advanced concepts is crucial for optimizing efficiency, controlling speed, and troubleshooting potential issues. This section explores the nuances of back EMF, armature reaction, commutation, and ultimately, how these factors shape the unique characteristics of different DC motor types.
Back EMF in DC Motors
Back electromotive force (back EMF) is a voltage generated within a DC motor that opposes the applied voltage. Its existence is a direct consequence of Faraday’s Law of Induction, which states that a changing magnetic field induces a voltage in a conductor. As the motor’s armature rotates within the magnetic field, conductors cut through magnetic flux lines, generating this opposing voltage.
Back EMF and Motor Speed
The magnitude of the back EMF (Eb) is directly proportional to the motor’s speed (N) and the magnetic flux (Φ) linking the armature windings. This relationship is mathematically expressed as: Eb = KΦN
, where K is a constant that depends on the motor’s construction. This equation reveals a fundamental link between the motor’s speed and the voltage generated within it.
Back EMF and Torque-Speed Characteristic
The back EMF plays a crucial role in shaping the motor’s torque-speed characteristic. At low speeds, the back EMF is low, allowing a large current to flow, resulting in high torque. As the speed increases, the back EMF increases, reducing the net voltage across the armature and thus the current and torque. This relationship is depicted in a typical torque-speed curve, which shows a roughly linear decrease in torque as speed increases.
Imagine a graph where the x-axis represents speed and the y-axis represents torque; the curve would slope downward, demonstrating the inverse relationship.
Back EMF and Starting Current
The back EMF acts as a natural current limiter during motor startup. When the motor is initially at rest (N=0), the back EMF is zero. However, as the motor accelerates, the back EMF increases, limiting the current flow and preventing potentially damaging surges. This inherent current limitation is a significant advantage, protecting the motor and associated circuitry.
Effect of Field Flux on Back EMF
Varying the field flux (Φ) at a constant speed directly impacts the back EMF. Increasing the field flux increases the back EMF, while decreasing the field flux reduces it. This principle is exploited in various speed control methods for DC motors. For example, reducing the field flux allows the motor to achieve higher speeds, while increasing the field flux allows for greater torque at lower speeds.
Effects of Armature Reaction
Armature reaction refers to the magnetic field distortion caused by the armature current’s own magnetic field. The armature, carrying a current, produces its own magnetic field which interacts with the main field produced by the field windings.
Armature Reaction and Field Flux
This interaction leads to a weakening and distortion of the main field flux. The armature’s magnetic field tends to oppose the main field in some areas and reinforce it in others, leading to an uneven distribution of flux across the air gap. A diagram would show the main field lines, usually depicted as smooth concentric circles, becoming distorted and pushed aside by the armature field lines.
Armature Reaction and Commutation
Armature reaction negatively affects the commutation process, the process of smoothly reversing the current in the armature windings. The uneven field distribution caused by armature reaction can lead to sparking at the commutator brushes, causing wear and tear and potential damage to the motor.
Compensation for Armature Reaction
Several methods are employed to compensate for armature reaction. One common method is the use of compensating windings. These windings, embedded in the pole faces, produce a magnetic field that counteracts the distorting effect of the armature field. A schematic diagram would show these compensating windings positioned in slots within the pole faces, their current flowing in a direction opposite to that of the armature current.
Armature Reaction in Different Motor Types
The effects of armature reaction vary among different DC motor types. In separately excited motors, the effect is relatively independent of the load current. In shunt motors, the effect is more pronounced at higher loads. In series motors, the effect is significant at all loads due to the high armature current.
Commutation in DC Machines
Commutation is the process of reversing the current in the armature conductors as they pass under the brushes. This process is essential for the continuous rotation of the DC motor and for preventing sparking.
Current Reversal in a Commutator Segment
The commutator, a segmented cylindrical structure, plays a vital role in this process. As a commutator segment passes under a brush, the current flowing through that segment is smoothly reversed, ensuring a continuous unidirectional torque. A detailed diagram would show the commutator segments, the brushes, and the current flow paths, illustrating the smooth transition of current from one segment to the next.
Reactance Voltage and Commutation
Reactance voltage is an induced voltage in the armature coils during commutation. This voltage opposes the current reversal, potentially leading to sparking and poor commutation.
Methods to Improve Commutation
Several methods improve commutation, including interpoles and compensating windings.
Method | Description | Advantages | Disadvantages |
---|---|---|---|
Interpoles | Small auxiliary poles placed between the main poles; they generate a magnetic field that helps neutralize the reactance voltage. | Reduces sparking, improves commutation, relatively simple to implement. | Adds complexity, requires careful design and adjustment. |
Compensating Windings | Windings embedded in the pole faces that counteract the distorting effect of the armature reaction. | Effectively reduces armature reaction, improves commutation and efficiency. | More complex and expensive to implement than interpoles. |
Importance of Good Commutation
Good commutation is crucial for efficient and smooth DC motor operation. Poor commutation leads to sparking, brush wear, and reduced motor efficiency. Severe cases can even damage the commutator and windings.
Comparative Analysis of DC Motor Types
Separately excited, shunt, and series DC motors exhibit distinct performance characteristics due to differences in their field winding configurations and how they interact with back EMF, armature reaction, and commutation. Separately excited motors offer excellent speed control and stable operation. Shunt motors provide relatively constant speed under varying loads but are susceptible to higher armature reaction at heavier loads. Series motors deliver high starting torque, ideal for applications needing high initial force, but exhibit unstable speed characteristics under light loads. The interplay of back EMF, which limits current and influences speed, armature reaction, which distorts the magnetic field and affects commutation, and the commutation process itself, all contribute to these unique performance profiles. The efficiency of each type is also influenced by these factors; losses due to poor commutation and armature reaction significantly impact overall efficiency.
Comparison with AC Machines
The journey into the world of electric motors has thus far focused on the intricacies of DC machines. Now, we draw a fascinating comparison with their AC counterparts, revealing the unique strengths and weaknesses of each, and ultimately, their suitability for diverse applications. Understanding these differences is crucial for engineers and technicians alike, allowing for informed decisions in the design and selection of motors for various tasks.
Detailed Operating Principle Comparison
The fundamental differences between DC and AC machines lie in how they generate torque and manage the flow of current. This comparison will illuminate these core distinctions, providing a clear picture of their operational mechanics.
Aspect | DC Machine | AC Machine |
---|---|---|
Torque Generation | Interaction between the magnetic field produced by field windings and the current-carrying armature conductors. The commutator ensures unidirectional torque. | Interaction between the rotating magnetic field of the stator and the induced currents in the rotor conductors. Torque is produced by the electromagnetic forces acting on the rotor. |
Commutator/Slip Rings | A commutator reverses the current direction in the armature windings, ensuring unidirectional torque. It is a mechanical device prone to wear and sparking. | Slip rings provide a continuous electrical connection to the rotating rotor windings. They are more robust than commutators but require careful maintenance. |
Magnetic Field Nature | Typically uses a stationary magnetic field generated by field windings interacting with a rotating armature. | Utilizes a rotating magnetic field generated by the stator windings interacting with a rotating rotor. |
Speed Control Methods | Speed is controlled by varying the field flux or armature voltage. Precise speed control is achievable. | Speed is controlled by varying the frequency or voltage of the AC supply. Methods include variable frequency drives (VFDs). |
Advantages and Disadvantages
The decision between a DC and AC motor often hinges on a careful weighing of their respective advantages and disadvantages. The following table highlights these key aspects, offering a quantitative perspective where possible.
Feature | DC Machine | AC Machine |
---|---|---|
Efficiency | Generally high efficiency at rated load, but can be lower at light loads. | High efficiency across a wide range of loads, particularly induction motors. |
Cost | Generally higher initial cost due to the commutator and associated components. | Lower initial cost, especially for induction motors. |
Maintenance | Higher maintenance requirements due to commutator wear and brush replacement. | Lower maintenance requirements, typically requiring less frequent servicing. |
Power Factor | Power factor is typically unity (1) for DC machines. | Power factor can be lagging, especially for induction motors, requiring power factor correction. |
Speed Control | Excellent speed controllability, particularly with sophisticated control systems. | Good speed controllability with VFDs, but less precise than DC motors in some cases. |
Starting Torque | High starting torque, typically 150-200% of rated torque. | Starting torque varies depending on the type of AC motor; induction motors generally have lower starting torque than DC motors. |
Application Suitability
The choice between DC and AC motors is heavily influenced by the specific application requirements. Let’s explore some examples where each type excels.
DC motors are particularly well-suited for applications requiring precise speed control and high starting torque. Examples include:
- Electric vehicles: DC motors provide excellent speed control and high torque for acceleration, making them ideal for electric car applications. The precise speed control is crucial for smooth operation and efficient energy management.
- Industrial robots: The need for precise positioning and controlled movements in robotic arms necessitates the precise speed and torque control offered by DC motors. This is essential for accurate and repeatable actions.
- Elevators and hoists: The high starting torque and precise speed control are critical for smooth and safe operation of elevators and hoists. This ensures a comfortable ride and prevents jerky movements.
AC motors, especially induction motors, are favored for their robustness, lower cost, and high efficiency. Examples include:
- Fans and pumps: Induction motors are simple, reliable, and efficient for constant-speed applications like fans and pumps. Their low maintenance requirements make them cost-effective over their lifespan.
- Industrial machinery: Many industrial machines utilize induction motors due to their ruggedness, relatively low cost, and ability to operate under harsh conditions. Their simple construction contributes to their reliability.
- Household appliances: The widespread use of induction motors in appliances like washing machines and refrigerators stems from their low cost, high efficiency, and relatively quiet operation. Their simplicity also contributes to ease of manufacturing.
Efficiency Analysis
A graphical representation of efficiency versus load would show a generally higher efficiency for AC induction motors across a broader load range compared to DC motors. DC motors often exhibit peak efficiency near their rated load, while efficiency drops off more significantly at lighter loads due to the constant losses associated with the commutator and brushes. AC induction motors, conversely, maintain relatively high efficiency even at partial loads.
This difference stems from the fundamental operational principles and the presence of mechanical losses in DC machines. (A graph would be included here if visual representations were allowed).
FAQ Guide
What are the practical implications of understanding electron flow in DC machines?
Understanding electron flow allows for improved design, more efficient operation, and more effective troubleshooting of DC machines. It enables engineers to optimize performance, minimize energy loss, and predict potential issues.
How does electron theory explain back EMF?
Back EMF is a direct consequence of Faraday’s Law of Induction. As the armature rotates within the magnetic field, the movement of electrons in the conductors generates a voltage that opposes the applied voltage. This opposing voltage is the back EMF.
What role do materials play in the electron flow within a DC machine?
The conductivity of the materials used in the armature windings and other components directly impacts the ease and efficiency of electron flow. Insulation materials prevent unwanted current paths, while the magnetic properties of the core materials influence the magnetic field strength.
How does temperature affect the performance of DC machines related to electron flow?
Increased temperature can reduce the conductivity of the materials, leading to increased resistance and reduced efficiency. Higher temperatures also impact insulation, potentially leading to short circuits and malfunctions.